The hydraulic system of the cone crusher is one of its key components. It is responsible for providing power and control to the crusher to ensure its normal operation and efficient crushing. The following is the basic composition and working principle of the cone crusher hydraulic system:
Component:
Hydraulic station: including motor, oil pump, oil tank, filter, etc., providing a stable source of hydraulic oil for the system.
Hydraulic cylinder: The pressure change of the oil generates thrust or pulling force, thereby driving the moving cone of the cone crusher to swing.
Control valve: including directional control valve, flow control valve and pressure control valve, etc., used to control the flow direction, flow and pressure of hydraulic oil to achieve precise control of the crusher.
Piping system: including oil pipes, joints, seals, etc., used to transport hydraulic oil from the hydraulic station to the hydraulic cylinder and control valve, and to recover the hydraulic oil back to the tank.
Working principle:
When the motor starts, the oil pump begins to suck oil from the oil tank and transports the oil through the pipeline to the hydraulic cylinder and control valve.
The control valve controls the flow direction and flow rate of hydraulic oil according to the operator's instructions or preset programs, thereby driving the hydraulic cylinder to perform telescopic movements.
The telescopic motion of the hydraulic cylinder drives the moving cone of the cone crusher to swing, causing the material to be impacted, squeezed and bent in the crushing chamber to achieve crushing.
During the crushing process, the hydraulic system controls the swing motion of the cone by adjusting the operating speed and direction of the hydraulic motor to adapt to the crushing needs of materials with different hardness and granularity.
The crushed materials are discharged through the discharge port, and the hydraulic system recovers the hydraulic oil back to the tank for recycling.
The hydraulic system of the cone crusher has the advantages of compact structure, sensitive movement, and precise control, which can achieve efficient crushing and precise control of materials. At the same time, the hydraulic system also has good overload protection and automatic adjustment functions, which can ensure the stable operation of the crusher and extend its service life.
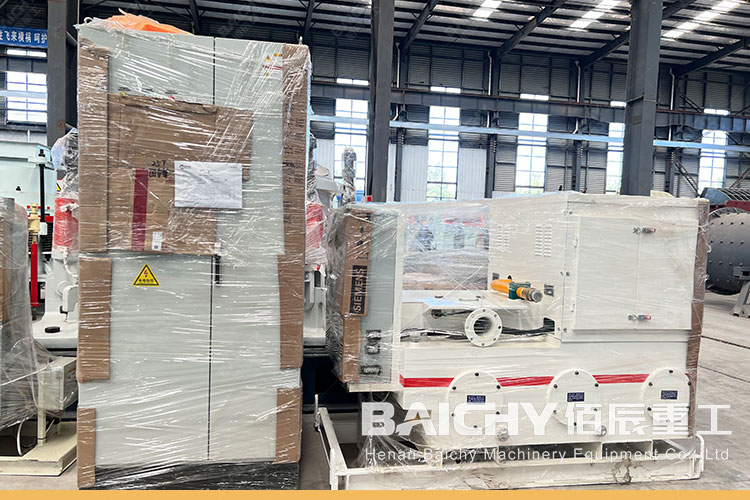
The maintenance and upkeep of the hydraulic system is key to ensuring its normal operation and extending its service life. The following are some recommended maintenance and upkeep measures:
Keep the system clean: Hydraulic systems should be kept clean to prevent contaminants from entering the system. Clean and inspect pipes, connections, and components regularly to ensure they are free of dust, dirt, or other impurities. The oil must be filtered before refueling, and the oil quality must be replaced and checked regularly.
Check seals and lines regularly: Seals and lines are leak-prone parts of a hydraulic system. The wear and aging of seals should be checked regularly and damaged seals should be replaced in a timely manner. At the same time, check whether the pipeline connections are tight to avoid looseness and leakage.
Regularly check component performance: The main components in the hydraulic system, such as pumps, motors, valves, etc., should have their performance measured regularly. If the performance of a component is found to be degraded or damaged, it should be repaired or replaced in time.
Check oil level and oil temperature regularly: Maintaining proper oil level and oil temperature is key to the proper operation of your hydraulic system. The oil level should be checked regularly to ensure that the oil is within the appropriate range. At the same time, pay attention to changes in oil temperature to avoid excessively high or low oil temperatures affecting system performance.
Pay attention to system starting and stopping: Before starting the hydraulic system, check whether each control component and electrical switch is in the normal position. When using the hydraulic system in winter, it should be started and stopped several times without load to allow it to heat up before entering the working state. After stopping the hydraulic system, adjust the control switches of each component to the normal position and cut off the power supply.
Check the solenoid valve regularly: The solenoid valve is one of the key components in the hydraulic system. The working status of the solenoid valve electromagnet should be checked regularly to ensure its normal operation. If it is found that the electromagnet has insufficient suction or abnormal heating, it should be repaired or replaced in time.
Regularly adjust the pressure of the relief valve: The relief valve is one of the safety components in the hydraulic system. Check regularly whether the rated pressure of the relief valve exceeds the maximum pressure of the hydraulic system and make appropriate adjustments. When the hydraulic pump starts or stops, the relief valve should be in an unloaded state.
Perform regular hydraulic oil cleanliness testing: The cleanliness of hydraulic oil has a great impact on system performance. Hydraulic oil cleanliness should be checked regularly and replaced or filtered as necessary. If serious oil contamination is found, it should be dealt with in time.
In short, the maintenance and upkeep of the hydraulic system is a comprehensive task that requires regular inspection, cleaning, replacement, and repair of various components. Through correct maintenance and upkeep measures, the normal operation and extended service life of the hydraulic system can be ensured.