Jaw crusher for limestone crushing plant
Jaw crusher is a device that crushes materials through the periodic movement of the movable jaw. When the movable jaw swings toward the fixed jaw around the hanging mandrel, the material between the two jaw plates is subjected to comprehensive effects such as crushing, splitting, and bending. The crushing cavity of the jaw crusher is deep and has no dead space, which improves the feeding capacity and output. At the same time, its crushing ratio is large and the product particle size is uniform. This kind of crusher has a simple structure, reliable operation, and low operating cost. It has been widely used in mining, construction, smelting, and other industries.
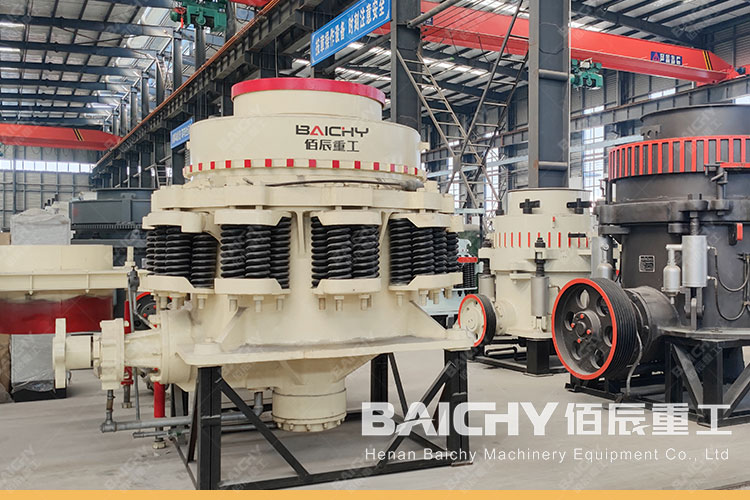
Cone crusher for limestone crushing plant
Cone crusher is especially suitable for crushing materials with medium hardness and above, such as limestone, granite, basalt, etc. Its working principle is to crush materials through the squeezing and shearing action between a rotating cone (moving cone) and a fixed cone (fixed cone). Cone crusher has the characteristics of a large crushing ratio, high efficiency, low energy consumption, and uniform product particle size. In addition, it can adapt to a wide range of material hardness and humidity, and its operation and maintenance are relatively simple.
Jaw crusher & Cone crusher have their own advantages when it comes to crushing limestone. Impact crusher is suitable for the production of construction aggregates, artificial sand, etc. due to its efficient crushing capacity and hard material processing capabilities. The jaw crusher, with its stable performance and low operating costs, is suitable for crushing needs of various sizes, especially in the mining and construction industries.
Both Cone crusher and jaw crusher have their own characteristics and advantages in crushing limestone. Which equipment to choose mainly depends on the specific production needs and material characteristics.
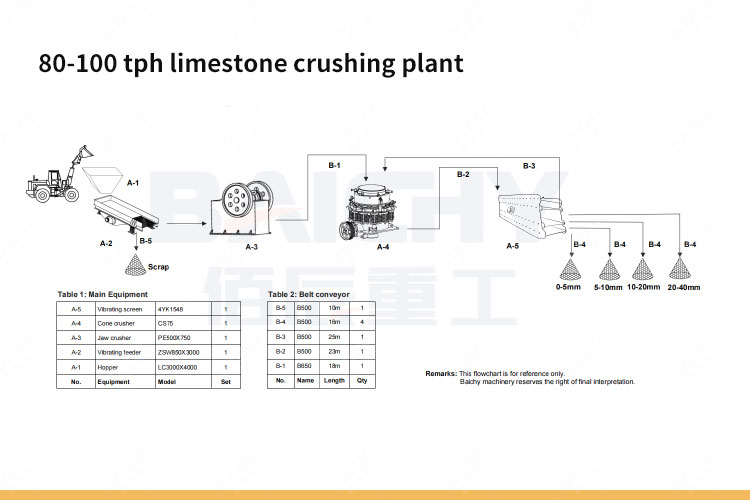
For limestone crushing requirements of 80-100t/h, the following options can be considered for equipment selection and configuration:
1. Raw material warehouse: First of all, there needs to be a large enough raw material warehouse to store the limestone to be crushed. The size of the warehouse should be determined based on the production cycle and raw material supply. LC3000x4000 is recommended.
2. Feeding equipment: You can choose a suitable vibrating feeder, such as the ZSW850x3000 vibrating feeder, which can evenly and continuously feed limestone from the raw material bin to the crusher.
3. Primary crushing equipment: For outputs of 80-100 tons/hour, a jaw crusher is a good choice. You can choose a PE series jaw crusher, such as the PE500x750 jaw crusher model, which has high crushing efficiency and stable performance.
4. Intermediate storage and conveying equipment: After primary crushing, an intermediate silo can be set up to store the crushed materials and transport the materials to the next level of crushing equipment through conveyor belts.
5. Secondary crushing equipment: According to the particle size requirements of the finished product, impact crusher or cone crusher (cs75 cone crusher) can be used as the secondary crushing equipment. Impact crushers are suitable for medium-hard materials and can produce better particle shapes and lower dust amounts; while cone crushers are more suitable for crushing harder materials.
6. Screening equipment: After crushing, the materials that meet the requirements need to be screened out by the screening equipment, and the materials that do not meet the requirements are sent back to the crusher for re-crushing. You can choose a 4YK series vibrating screen, such as model 4YK1548.
7. Conveying equipment: During the entire production process, multiple conveyor belts are needed to connect various equipment to ensure the smooth flow of materials.
8. Control system: In order to ensure the stable operation of the entire production line, a complete electrical control system needs to be configured to centrally control, monitor, and protect the equipment.
It should be noted that the above equipment selection and configuration are for reference only. The specific configuration needs to be comprehensively considered based on actual production needs, material characteristics, site conditions, and other factors. When selecting equipment, it is recommended to consult a professional crushing equipment manufacturer or technician to ensure the accuracy and rationality of equipment selection.