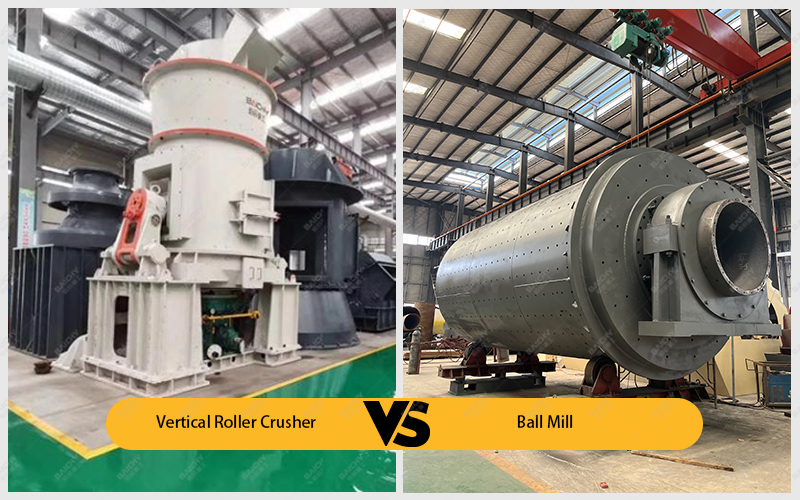
What is the expected lifespan of a VRM?
The life expectancy of a vertical roller mill is not a fixed value because it is affected by many factors. Among them, the hardness, particle size, moisture content, and grindability of the grinding materials are all key factors. Generally speaking, grinding materials with high hardness, large particle size, improper moisture content control, or poor grindability will increase the wear of the grinding roller and shorten the service life of the equipment.
In addition, equipment maintenance and upkeep also have a significant impact on life expectancy. Regularly adding lubricating oil, checking the bearing temperature, replacing seriously worn blades or grinding rollers, grinding rings, and other wearing parts, as well as keeping the motor and conveying equipment clean and well-ventilated are all effective measures to extend the life of the equipment.
Can the VRM be used for grinding other materials besides cement?
Yes, vertical roller mills can be used to grind other materials besides cement. This kind of equipment is mainly used for the grinding and processing of cement raw materials, cement clinker, slag, and cinder. It has the characteristics of a simple structure and low manufacturing and use costs. It can grind a wide range of materials, from high-humidity to dry materials, such as calcium carbide slag and clinker cement, to extremely difficult-to-grind to easy-to-grind materials, such as quartz sand and gypsum, etc., and can be effectively processed.
In addition, the vertical roller mill also has the characteristics of low wear and a high utilization rate. The wear per unit product is generally 5~10g/t. The life of the roller sleeve and liner is more than 8,000 hours, and the operation rate can reach 95%. These advantages make vertical roller mills an ideal choice for key national infrastructure construction projects such as cement, mining, construction, and energy.
What are the maintenance requirements for a VRM?
The maintenance requirements of vertical roller mills mainly include the following aspects:
1. Maintenance of grinding roller and grinding ring: The grinding roller and grinding ring are the main wear parts of the vertical roller mill, and they will gradually wear out after long-term use. Therefore, it is very necessary to regularly check the wear of the grinding roller and grinding ring. Once serious wear is found, it should be replaced in time. In addition, to extend their service life, the grinding roller and grinding ring need to be lubricated and maintained regularly.
2. Maintenance of bearings: Bearings are one of the important wearing parts of vertical roller mills. Lubricating oil must be added regularly to ensure smooth operation of the bearings and avoid overheating of the bearings. At the same time, check the bearing temperature regularly to ensure that it does not exceed the normal range.
3. Lubrication and sealing: The bearing seal of the vertical roller mill is connected to the atmosphere outside the mill, so there is no need to configure a sealing fan. However, it is still necessary to ensure that all parts of the equipment are well-lubricated to reduce wear. At the same time, check whether the nuts and bolts are loose and tighten them in time to ensure the normal operation of the equipment.
4. Maintenance of electrical equipment and safety facilities: Regularly check the wires and cables of the machine and replace them if they are damaged. Regularly check the grounding of electrical equipment to ensure good grounding to prevent electrical accidents. In addition, it is necessary to regularly check and clean the oil stains, remove sludge and impurities, ensure the cleanliness of the oil, and replace the engine oil regularly.
5. Precautions when shutting down: When shutting down, the feeding device, main motor, grinding system, separator, hydraulic oil pump, and lubricating oil pump should be stopped in the specified order to avoid equipment damage.
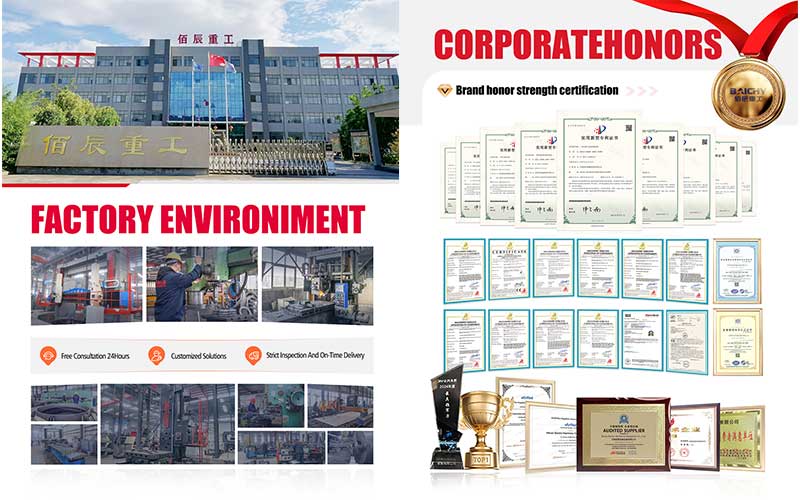
Baichy Heavy Industry – Your Trusted Partner for Seamless Equipment Operation
To ensure optimal performance of your equipment, Baichy Heavy Industry offers:
- Professional on-site installation guidance
- Comprehensive operator training
- 24/7 technical support & maintenance services
Our complete after-sales service system guarantees long-term, stable operation of your machinery with minimal downtime.
Protect Your Rights – Only Use Official Channels
To avoid scams and ensure authentic support, contact us exclusively through:
• Official Website: www.baichychina.com
• WhatsApp: +8615093222637
• Email: [email protected]
Your satisfaction is our priority – expect prompt, professional service every time.
(Note: Beware of unauthorized third parties claiming to represent Baichy. Always verify through official contacts.)
Further reading:
How To Reduce The Energy Consumption Of Ball Mill? 5 Practical Energy-Saving Tips
How To Improve Ball Mill Efficiency? 5 Practical Tips
Ball Mill Maintenance Guide : 10 Key Methods To Extend Life
How To Choose A Suitable Ball Mill Model?