In response to the demand for 9-22tph (tons per hour) Raymond mill for producing limestone containing 90% CaCO₃, the following is a summary and explanation of the relevant information of Raymond mill:
Overview of Raymond mill
Raymond mill is a commonly used grinding equipment, mainly used for high-fine grinding of non-flammable and explosive materials with a Mohs hardness not greater than a certain level (usually below level 8 or 9.3) and a humidity below 6%. It has a wide range of applications, including mining, chemical industry, metallurgy, building materials, etc., and is particularly suitable for grinding materials such as limestone.
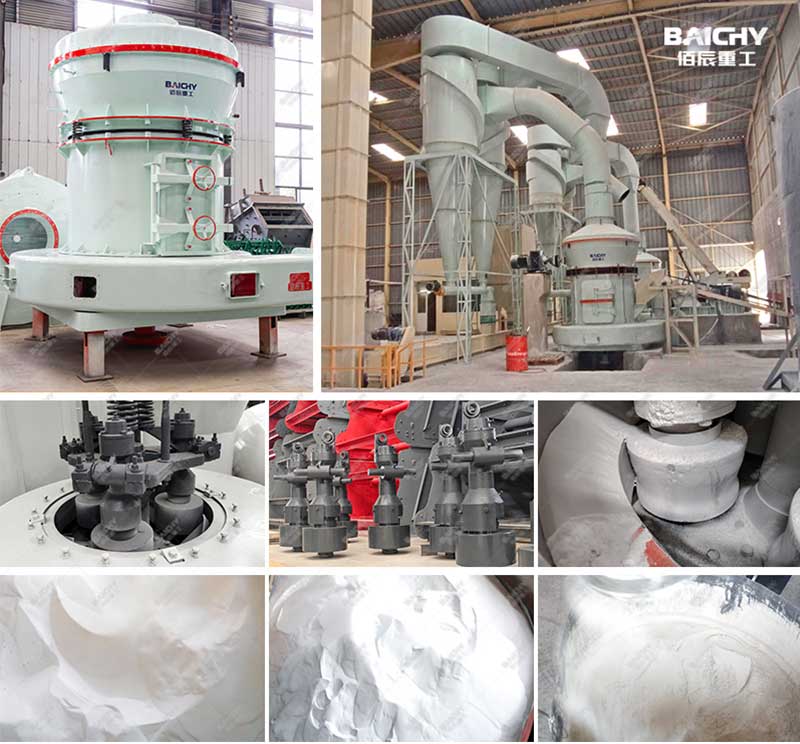
Technical parameters of Raymond mill
For 9-22tph Raymond mill, its technical parameters may vary depending on the brand and model, but usually include the following aspects:
1. Feed particle size: refers to the maximum particle size of the raw material before it enters the mill. The feed particle size of the Raymond mill is related to the angle between the grinding roller and the grinding ring, which is usually determined by the diameter of the grinding roller. According to the empirical formula, the relationship between the maximum feed particle size σ and the roller diameter d is σ=0.135d, but in actual operation, the size of the material should be about 20% smaller than the calculated value, that is, σ=0.11d.
2. Production capacity: that is, the output of the mill, usually in tons per hour (tph). For 9-22tph Raymond mills, the production capacity is within this range.
3. Motor power: refers to the motor power of the mill host, which determines the energy consumption and power of the mill. Raymond mills of different models and specifications may have different motor powers.
4. Finished product particle size: refers to the fineness of the material after grinding by the mill. The finished product particle size of the Raymond mill is adjustable, usually by adjusting the screen aperture or vibration frequency of the classifier. For the production of limestone containing 90% CaCO₃, it is necessary to determine the appropriate finished product particle size based on the specific application field and product quality requirements.
Raymond mill working process
The working process of Raymond mill usually includes the following steps:
1. Raw material crushing: The limestone raw material is crushed by a crusher and converted into small pieces.
2. Material transportation: The crushed material is sent to the Raymond mill for grinding by an elevator.
3. Grinding process: The material is subjected to mechanical force between the grinding roller and the grinding ring and gradually ground into fine powder.
4. Classification: The ground material is classified by a classifier to separate products of different fineness.
5. Dust collection: Dust is collected by dust removal equipment to ensure that the production process is environmentally friendly.
Precautions
1. Material characteristics: The hardness, humidity and other characteristics of limestone have an important influence on the grinding effect and energy consumption of the Raymond mill. Therefore, when choosing a Raymond mill, the characteristics of the material need to be fully considered.
2. Equipment selection: According to the production capacity and the requirements of the finished product particle size, select the appropriate Raymond mill model and specifications.
3. Maintenance: Regularly perform maintenance on the Raymond mill, including cleaning the accumulated powder on the grinding roller, grinding ring and other parts, checking whether the fasteners of the equipment are loose, etc., to ensure the normal operation of the equipment and extend its service life.
4. Environmental protection requirements: During the production process, effective dust removal measures need to be taken to reduce dust emissions and reduce environmental pollution.
9-22tph Raymond mill is suitable for the production of limestone containing 90% CaCO₃, but the specific selection and technical parameters need to be comprehensively considered according to the material characteristics, production capacity, finished product particle size and other requirements. At the same time, attention should be paid to maintenance and environmental protection requirements during use.