Overview of the configuration scheme for the production line with a final rock size of 800 mesh grinding mill
The rock grinding production line is mainly composed of feeder, hopper, jaw crusher, cone crusher, belt conveyor, vibrating screen and grinding mill (reaching 800 mesh fineness). Each device works together to complete the rock crushing, screening and grinding tasks.
Main equipment and its functions
1. Feeder
Function: Feed rock raw materials into the jaw crusher evenly and continuously.
Features: Adjustable feeding amount to ensure stable operation of the crusher.
2. Hopper
Function: Store and buffer rock raw materials to ensure continuous feeding of the production line.
Features: Simple structure and easy maintenance.
3. Jaw crusher
Function: Preliminary crushing of large rocks into smaller particles.
Features: Large crushing ratio and strong processing capacity.
Recommended model: PE750×1060, etc. The specific model needs to be determined according to production needs.
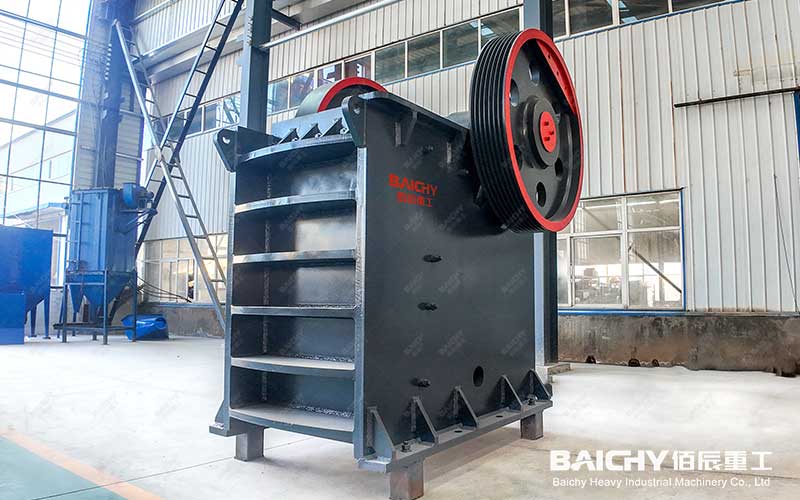
4. Cone Crusher
Function: Further crush the rock after the jaw crusher to meet the particle size requirements of the mill.
Features: High crushing efficiency and uniform finished product particle size.
Note: The specific model and configuration of the cone crusher should be determined according to the hardness of the rock and the requirements of the mill.
5. Belt Conveyor
Function: Connect various crushing and screening equipment to achieve continuous rock transportation.
Features: Strong conveying capacity and stable operation.
Quantity: Determined according to the production line layout and equipment spacing, usually multiple units are required.
6. Vibrating Screen
Function: Screen the rock after the cone crusher to separate the rock particles that meet the particle size requirements of the mill.
Features: High screening efficiency and easy maintenance.
Recommended configuration: Multi-layer vibrating screen to meet the screening needs of rocks of different particle sizes.
7. Mill
Function: Grind the screened rock particles into 800 mesh fine powder.
Features: High grinding efficiency and uniform finished product fineness.
Recommended models: HCH ultrafine roller mill or HLMX ultrafine vertical mill, etc. The specific model needs to be determined according to production needs and raw material characteristics.
Production line layout and process
1. The rock raw material is fed into the hopper by the feeder, and then evenly fed into the jaw crusher by the hopper for preliminary crushing.
2. The crushed rock particles are sent to the cone crusher by the belt conveyor for further fine crushing.
3. The finely crushed rock particles are screened by the vibrating screen to separate particles that meet the particle size requirements of the mill.
4. The screened rock particles are sent to the mill by the belt conveyor for grinding.
5. The fine powder after grinding is discharged from the discharge port of the mill, collected and stored.
Precautions
When selecting equipment, the hardness, humidity and abrasiveness of the rock must be fully considered to ensure the normal operation and grinding efficiency of the equipment.
The layout of the production line must be reasonable to ensure smooth connection between the equipment and reduce losses and energy consumption during material transportation.
During the production process, the equipment needs to be regularly maintained and serviced to ensure long-term stable operation of the equipment.
This configuration can meet the production needs of a final rock size of 800 mesh mill. However, please note that the selection and configuration of specific equipment should be determined based on actual production needs and raw material characteristics.