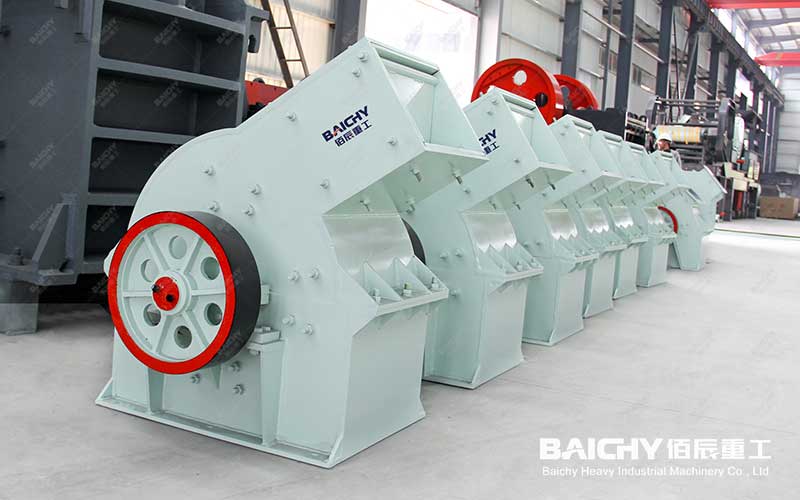
What is the working principle of a hammer crusher?
1. The motor drives the rotor to rotate at high speed through a V-belt and a large pulley.
2. The material to be crushed is fed evenly by the feeding equipment and sent into the crushing chamber. The high-speed rotating rotor drives the hammer to strike the material for the first time, and the material is crushed by the impact of the hammer.
3. After gaining kinetic energy, the material hits the impact plate at high speed or the material blocks collide with each other and are crushed again. During the collision, the material gradually moves to the movable impact plate at the bottom of the crushing chamber.
4. When the material size is smaller than the gap between the hammer and the movable impact plate, it will be separated from the crushing chamber under the pressure of its own weight and other materials and discharged from the lower hopper. The material goes through multiple crushing processes in the crushing chamber, such as iron hitting stone, stone hitting stone, and stone hitting iron.
According to the discharging particle size, the user can adjust the discharging particle size by adjusting the size of the discharging port gap. Some materials larger than the selected standard are screened by the screening equipment and sent back to the crusher for the next crushing cycle.
Internal structure of hammer crusher
The internal structure of hammer crusher is compact and complex, mainly including the following key components:
1. Frame: Also known as hammer crusher casing, it consists of lower body, rear upper cover, left wall and right wall, and the parts are connected as one by bolts. The frame is inlaid with high manganese steel lining to protect the casing and facilitate replacement. The lower body is welded with carbon structural steel plates, and a bearing support is provided to support the rotor.
2. Transmission device: It mainly consists of motor, elastic coupling and main shaft. The motor directly drives the main shaft to rotate through the elastic coupling, and the main shaft is installed in the bearing seats on both sides of the frame through spherical self-aligning ball bearings.
3. Rotor: It is the main working part of the hammer crusher, consisting of main shaft, hammer disc, pin shaft and hammerhead. The hammer head is suspended on the hammer disc through the pin shaft, and the main shaft is supported on the casing through the self-aligning rolling bearing. The rotor rotates at high speed driven by the motor, driving the hammer head to crush the material.
4. Hammer: It is the main force of crushing materials. Its quality, shape and material have a great impact on the production capacity of the equipment. The hammer is a consumable part and needs to be replaced frequently. In order to reduce the replacement time and labor intensity, a combined hammer is generally used.
5. Impact liner: When the hammer crusher is running, the impact liner will be impacted and ground by the material. It is cast with high manganese steel and strengthened to ensure its superior wear resistance and impact resistance.
6. Screen plate: It consists of an arc screen frame and a screen plate, which is set below the rotor. The main function of the screen plate is to allow qualified products to be discharged through the gap while controlling the particle size of the material. The gap of the screen plate gradually expands and tilts downward to facilitate the discharge of materials.
In addition, the hammer crusher also contains some other auxiliary components, such as adjustment devices, distributors, lubrication systems, etc., which work together to ensure the crusher's normal operation and crushing.
Technical parameters of hammer crusher
1. The specifications of the hammer crusher are usually expressed by the diameter D of the hammer end and the length L of the rotor. The ratio of the rotor diameter to its length is usually 0.5~0.8.
2. The speed of a single-rotor hammer crusher is generally 500600 rpm, while the speed of a double-rotor hammer crusher is 210300 rpm.
3. The circumferential speed of the rotor is generally 25~55 m/s.
4. The impact of the hammer is to convert its kinetic energy into work to break the material block, which is proportional to the weight of the hammer and the square of the circumferential speed of the hammer.
5. The humidity of the feed shall not exceed 15%, and the material size shall not be greater than 800~1000 mm.
6. The product size of a single-rotor hammer crusher is 2.510 mm, and the crushing ratio is generally 1015; while the product size of a double-rotor hammer crusher is 2030 mm, and the crushing ratio can reach 3040.
Advantages and Disadvantages of Hammer Crusher
1. Advantages:
• High production capacity.
• Large crushing ratio.
• Simple structure and compact machine size.
• Low power consumption.
• Simple maintenance during operation, easy repair and replacement of parts.
• Uniform product size and less over-crushing.
2. Disages:
• The hammer head is subject to greater wear and tear from the material and needs to be replaced regularly.
• For particularly hard or special rocks, more powerful equipment or other crusher models may be required to effectively handle them.
Application scope of hammer crusher
1. Mining and quarrying: used to process various hard rocks and ores, such as granite, limestone, coal, iron ore, etc.
2. Construction waste processing: used to process construction waste such as concrete, bricks, tiles, etc., and crush them into recycled aggregates for re-construction or recycling.
3. Road construction: crush rocks and other raw materials into particles or gravel suitable for paving.
4. Industrial sector: In cement, chemical, electric power, metallurgy and other industrial sectors, it is used to crush medium-hard materials such as limestone, slag, coke, coal, etc.
5. Waste treatment and recycling: It is used to treat various wastes such as furniture, glass, metal and wood, and crush them into appropriate particles for recycling or reuse.
Hammer crushers play an important role in many industries due to their high efficiency, energy saving and easy maintenance. When selecting and using hammer crushers, it is necessary to make appropriate selections and adjustments according to the specific material characteristics and production needs.
Perfect after-sales service
Baichy Heavy Industry provides professional on-site guidance for installation, training of workers, and other services to ensure that customers can use the equipment smoothly.
The company has a complete after-sales service system, which can provide customers with timely technical support and equipment maintenance services to ensure the long-term stable operation of the equipment.
To prevent the rights and interests of customers from being infringed, Baichy Heavy Industry reminds customers: please contact our customer service staff through the official website of Baichy Heavy Industry , or add WhatsApp: 15093222637 ; or send an email to: [email protected] , we will get in touch with you as soon as possible and provide you with the most professional service in the industry.
Further reading: