In view of the production demand of small limestone mill suitable for 45 mesh (about 0.35 mm), the following are detailed selection suggestions and precautions to help you achieve your goals efficiently and economically:
Equipment selection points/suitable model recommendation:
• Raymond mill:
Advantages: compact structure, low energy consumption, suitable for small and medium production capacity (0.5-5 tons/hour), flexible adjustment of 45 mesh, good dust control.
Applicable scenarios: small and medium-sized building materials factories, paint factories, chemical filler production.
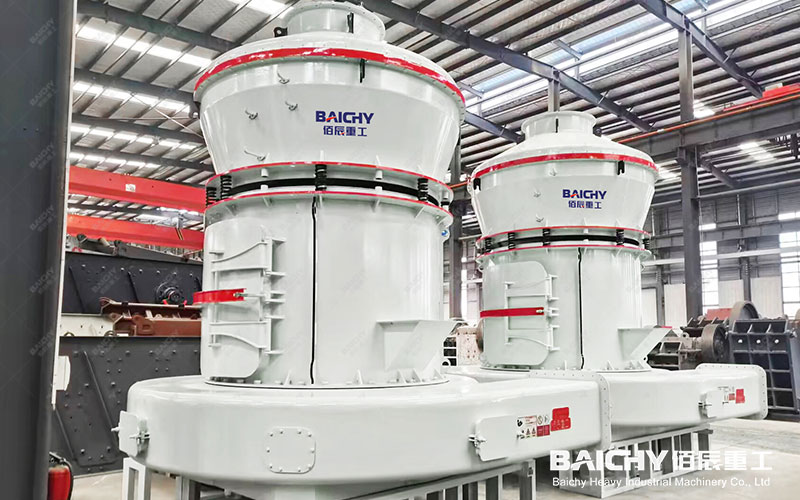
• High-pressure suspension roller mill:
Advantages: Stronger crushing force than Raymond mill, suitable for medium hardness limestone, and can take into account both coarse powder and fine powder needs.
Note: The equipment price and energy consumption are slightly higher than Raymond mill.
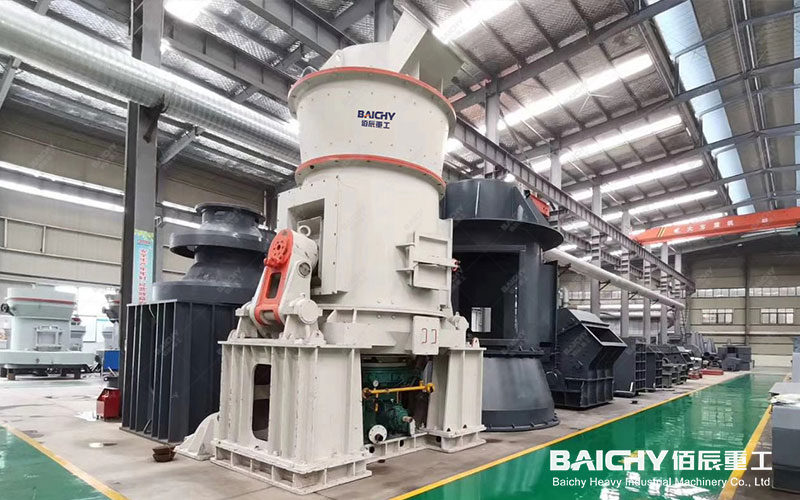
• Vertical mill (small model):
Advantages: Both dry and wet materials can be processed, energy-saving and environmentally friendly, but the initial investment is high, suitable for long-term stable production.
Equipment selection points/key parameter verification:
· Feed particle size: Ensure that the size of limestone raw materials is ≤25 mm (if the raw materials are too large, they need to be pre-processed with a jaw crusher).
· Finished product fineness: Confirm that the equipment can be adjusted within a range of 40-100 mesh (avoid reaching it barely and causing low efficiency).
· Motor power: Small machines are usually 15-30kW, which needs to match the local power grid capacity.
· Floor space: Raymond mills are about 5-10 square meters, and vertical mills require higher space.
Particle size adjustment and optimization/adjustment method:
· Analyzer speed: The higher the speed, the finer the powder. 45 mesh usually requires a medium speed gear, which needs to be fine-tuned according to the equipment manual or manufacturer's instructions.
· Air volume control: Increasing the air volume can increase the output of fine powder, but the classification efficiency needs to be balanced to avoid coarse powder.
• Replace the screen (if it is a ball mill): Choose a 45-mesh (aperture 0.35mm) screen and check for damage regularly.
Solutions to common problems:
• The finished product is too coarse: Check the wear of the analyzer blades, adjust the speed or reduce the feed speed.
• Output decreases: The grinding efficiency may be reduced due to the wear of the grinding roller and grinding ring, and the wearing parts need to be replaced in time.
Cost and maintenance/investment cost:
• Small Raymond mill: about 50,000-150,000 yuan (depending on the brand and configuration).
• Ball mill: The price is relatively low (30,000-80,000 yuan), but the energy consumption and maintenance costs are high.
Maintenance points:
• Life of wearing parts: Grinding rollers and grinding rings generally need to be replaced every 300-500 hours. Choosing high manganese steel material can extend the service life.
• Lubrication system: Check the lubrication of the grinding roller bearings regularly. It is recommended to add high-temperature resistant lithium-based grease every shift.
• Dust collector cleaning: The pulse bag dust collector needs to be cleaned every 2-3 days to prevent blockage and affect the air volume.
Environmental protection and safety
• Dust control:
A pulse bag dust collector (efficiency> 99%) must be equipped to ensure that the dust concentration in the workshop is <10mg/m³.
It is recommended to configure a closed conveying system to reduce dust in the feeding and discharging links.
• Noise protection:
The equipment noise is usually 85-90 decibels, and the operator needs to wear earplugs or install a soundproof cover.