According to your needs (capacity 6-8tph, calcium carbonate grinding), combined with equipment performance, fineness range and cost-effectiveness, the following are targeted recommendations:
1. YGM190 high-pressure suspension roller mill
Core advantages of YGM190 high-pressure suspension roller mill:
① Capacity: 6-8tph (fineness 80-425 mesh), perfectly matching your production needs.
② Fineness adjustment: supports 80-425 mesh (0.175-0.033mm), suitable for medium and fine powder scenes such as plastics and coatings.
③ Energy saving and durability: unit power consumption is reduced by 20%, and the life of high chromium alloy grinding roller is more than 3000 hours.
④ Environmental protection: pulse dust removal system, dust emission ≤30mg/m³, in line with environmental protection standards.
Applicable scenarios of YGM190 high-pressure suspension roller mill:
Calcium carbonate, limestone, talc and other medium and low hardness materials, pursuing cost-effective medium and fine powder processing.
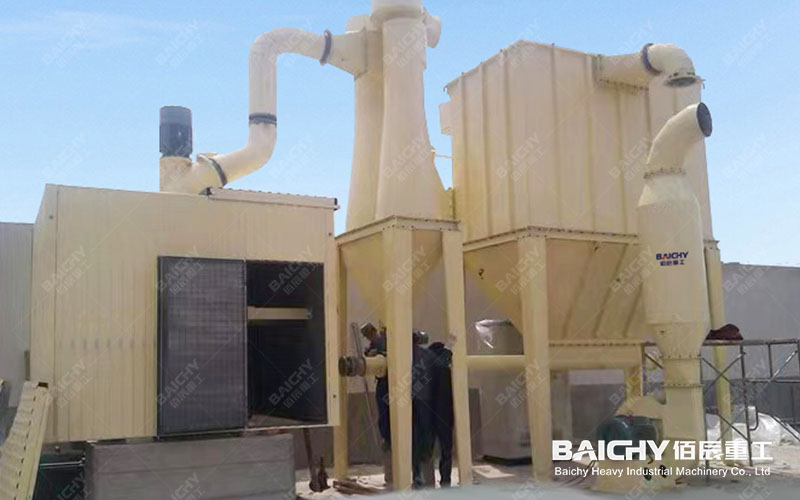
2. HGM1036 Ultrafine Vertical Mill
Core advantages of HGM1036 Ultrafine Vertical Mill:
①Production capacity: 1.2-11.5tph (fineness 325-3000 mesh), taking into account both high yield and ultrafine powder needs.
②Wide coverage of fineness: single machine can achieve coarse powder to fine powder (5-45μm), without secondary sorting.
③Intelligent control: PLC automatically adjusts grinding pressure and wind speed, and the stability of finished products is improved by 30%.
④Low maintenance cost: modular design of grinding rollers, replacement time is shortened to 8 hours.
Applicable scenarios of HGM1036 Ultrafine Vertical Mill:
High value-added calcium carbonate powder (such as papermaking, pharmaceutical grade), high-end market requiring ultrafine powder (D97≤5μm).
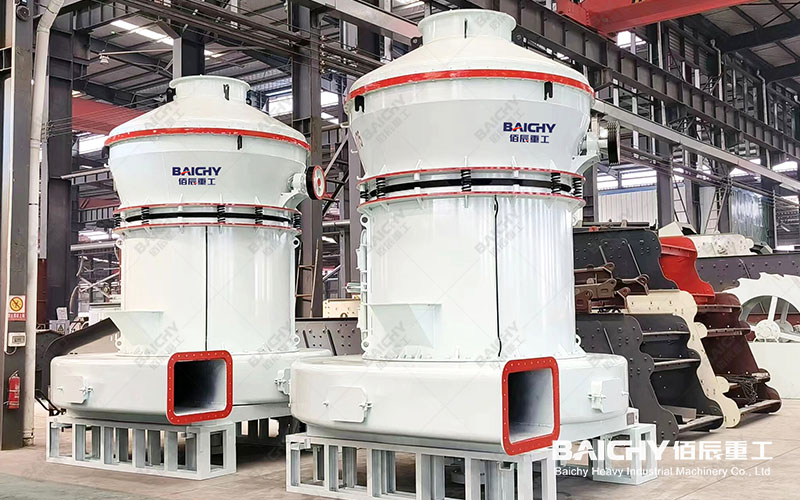
3. MTW215 European version mill
MTW215 European version mill core advantages:
① Capacity: 7-12tph (fineness 1.6-0.045mm), breaking through the bottleneck of traditional Raymond mill capacity.
② Efficient classification: bevel gear transmission classifier, the accuracy is 15% higher than that of traditional models.
③ Small footprint: three-dimensional structure design, saving 30% of plant space.
④ Outstanding cost performance: The investment cost is lower than that of ultra-fine vertical mill, suitable for medium and large projects with limited budget.
MTW215 European version mill applicable scenarios:
200-400 mesh calcium carbonate powder large-scale production (such as building materials, rubber fillers).
Selection comparison suggestions
Parameters | YGM190 high pressure suspension roller mill | HGM1036 ultrafine vertical mill | MTW215 European mill |
Applicable | fineness 80-425 mesh | 325-3000 mesh | 80-400 mesh |
Unit power consumption | Low (★☆☆) | Medium (★★☆) | Low (★☆☆) |
Investment cost | 300,000-500,000 | 800,000-1.2 million | 500,000-700,000 |
Maintenance complexity | Simple (replace roller/ring) | Medium (requires professional team) | Simple (modular design) |
Best scenario | Medium-fine powder | fast return on investment Ultrafine powder | high added value Medium-fine powder, large-scale production |
Recommendation summary
Budget limited, pursuit of stable returns → YGM190 high pressure suspension roller mill (price-performance ratio preferred).
Production of ultrafine powder (above 3000 mesh) → HGM1036 ultrafine vertical mill (leading technology, high added value).
Massive production (200-400 mesh) → MTW215 European mill (high efficiency, energy saving, easy maintenance).
Act now:
Provide free material trial grinding service! Submit your calcium carbonate sample and get a customized selection report + cost analysis within 24 hours.
Contact engineer: 15093222637
Email: [email protected]
Tips: If the humidity of calcium carbonate raw materials is > 6%, it is recommended to use a rotary dryer to ensure grinding efficiency and finished product quality!