Considering the need for a 120-150 tph impact crusher plant to produce three types of aggregates, 0-5mm, 5-10mm, and 10-20mm, the optimization configuration plan and implementation suggestions are as follows:
120-150tph impact crusher production line equipment selection and configuration
• Coarse crushing stage: Use jaw crusher (such as PE600×900) to process large pieces of raw materials (≤500mm), the discharge particle size is ≤150mm, and the output is 150-200t/h, providing uniform feed for subsequent impact crushing.
• Medium and fine crushing stage: Use 2 impact crushers (such as PF-1315 or VSI1140), with a single processing capacity of 80-120t/h, adjust the rotor speed and the gap between the impact plates, and control the discharge particle size ≤30mm. Impact crushing has both shaping function and can improve the quality of aggregate particles.
• Sand making adjustment: If the demand for 0-5mm accounts for a high proportion, a vertical shaft impact crusher (sand making machine) can be added, which is dedicated to fine crushing and sand making to increase the output of fine aggregate.
• Multi-layer vibrating screen: Equipped with 3YK3070 three-layer circular vibrating screen (processing capacity 150-200t/h), the screen holes are 20mm, 10mm, and 5mm respectively, to achieve precise classification:
• Upper layer (>20mm): return to the impact crusher for closed-loop circulation;
• Middle layer (10-20mm): directly as finished product;
• Lower layer (5-10mm): part of the finished product, ultra-fine material enters the lower layer;
• Bottom layer (0-5mm): finished sand.
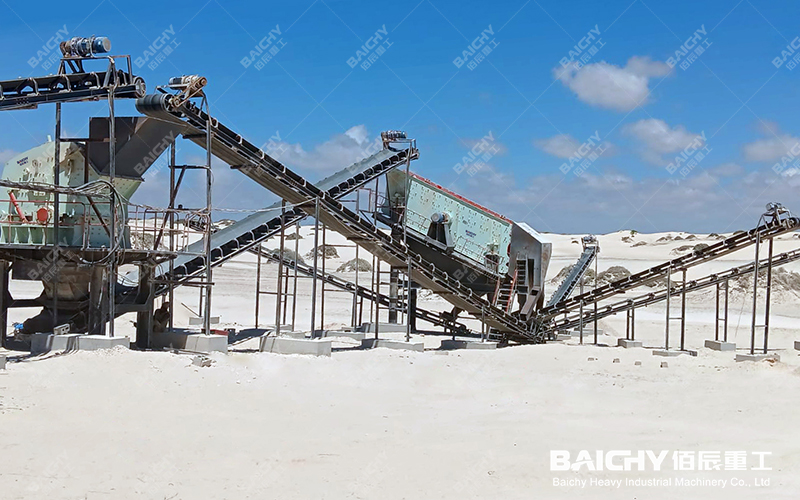
•Return system: set up a belt conveyor to return unqualified materials to the impact crusher to form a closed-loop circulation, improve efficiency and reduce waste.
Auxiliary equipment
·Feeder: ZSW490×110 vibrating feeder, evenly feeds the jaw crusher, with a processing capacity of 200-350t/h.
·Conveyor: Belt conveyor with a bandwidth of 800-1000mm, with smooth connection between each link.
·Dust removal system: Pulse bag dust collector is configured at the crushing and screening point to ensure dust emission <20mg/m³.
Process optimization of 120-150tph impact crusher production line
Flexibly respond to changes in market demand by adjusting the screen inclination or replacing the screen (such as replacing 5mm screen with 6mm). If the demand for 10-20mm increases, the upper screen hole can be appropriately increased to reduce the amount of return material.
An adjustable baffle is installed at the discharge port of the impact crusher to control the distribution of materials entering the screening and indirectly adjust the output of each specification.
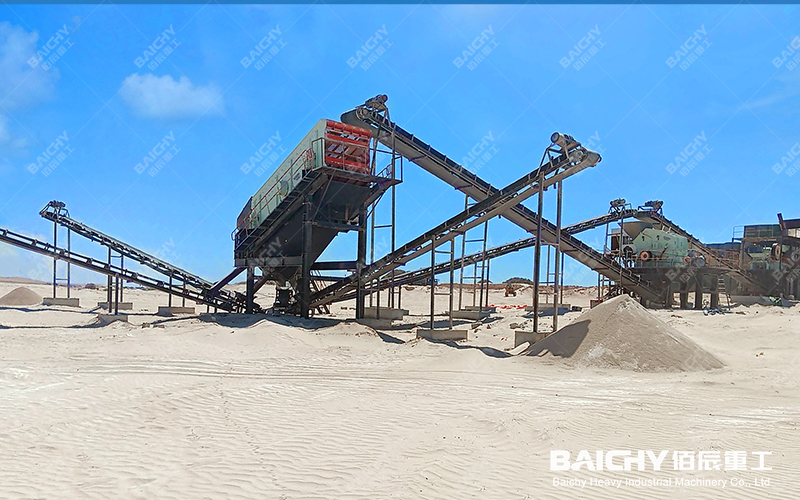
120-150tph impact crusher production line wear-resistant parts and maintenance strategy
• High chromium alloy hammer and impact block are used to extend the service life to 80-120 hours (such as granite processing).
• Regularly monitor the wear of the screen and check the blockage of the screen holes every shift to ensure that the screening efficiency is greater than 90%.
Energy saving and cost control
• Configure a frequency converter to control the impact crusher motor, automatically adjust the speed according to the load, and reduce power consumption by 10%-15%.
• Centralized lubrication system to reduce labor maintenance costs and improve equipment operation stability.
Calculation of production capacity and product ratio
0-5mm | 40% | 60t/h |
5-10mm | 30% | 45t/h |
10-20mm | 30% | 45t/h |
Note: The actual ratio can be dynamically adjusted by adjusting the screening parameters and the amount of return material.
Implementation points of 120-150tph impact crusher production line
• Site layout: Adopt "Z" type stepped layout, use height difference to reduce transportation energy consumption, ensure that the distance between each device is ≥5 meters, and facilitate maintenance.
• Inspection and debugging: After 4 hours of no-load operation, gradually load, monitor parameters such as vibration and temperature, adjust the amplitude of the screen machine to 3-5mm, and ensure uniform distribution of materials.
• Environmental compliance: equipped with a soundproof cover (noise reduction of more than 25dB) and a rainwater collection system to meet green
120-150tph impact crusher production line expected return on investment
• Equipment investment: about 3-4 million yuan (including jaw crusher, impact crusher, screening machine, conveying system, etc.).
• Operating cost: power consumption is about 35-45kW·h/ton, and the annual cost of replacing wear-resistant parts is about 500,000 yuan.
• Payback period: based on the average price of aggregate of 60 yuan/ton and 300 days of operation per year, the annual output value is about 64.8 million yuan, and the investment payback period is about 8-12 months.
Through the above configuration and optimization, the production line can stably achieve an annual output value.