Selection of core equipment for a stone crushing plant capable of crushing 100,000 tons of limestone per year
1.Coarse crushing stage (primary crushing)
• Recommended equipment: steam crusher (PE series or C series)
• Example: PE600×900 (processing capacity 50-160t/h, feed size ≤500mm)
• Advantages: simple structure, low maintenance cost, suitable for processing large pieces of limestone, high crushing ratio.
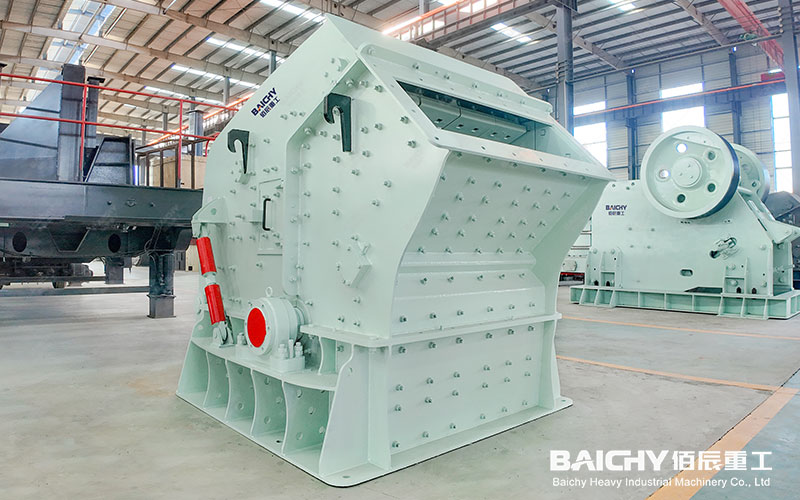
2.Middle crushing stage (secondary crushing)
Option 1: Impact crusher (PF series)
• Applicable scenarios: high requirements for finished product particle shape (such as building aggregates), medium transparency of limestone.
• Model example: PF1214 (processing capacity 80-180t/h, discharge particle size can be adjusted to ≤30mm)
• Advantages: discharge is cubic, less over-crushing; Disadvantages: hammer fatigues quickly and needs to be replaced regularly.
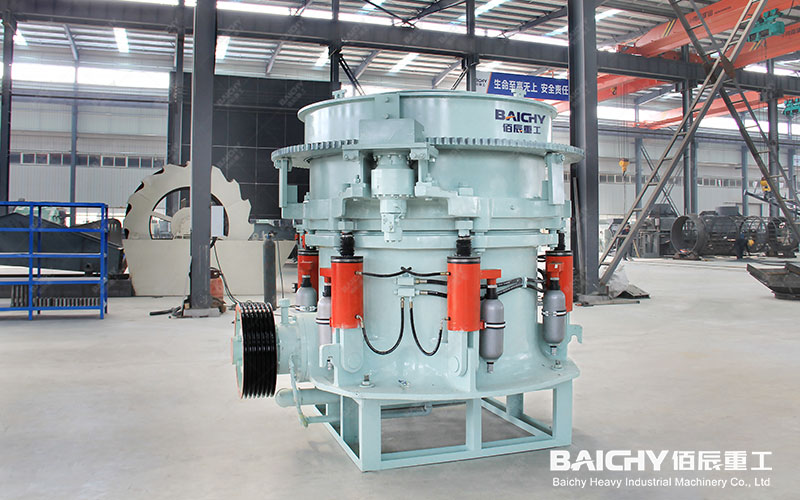
Option 2: Cone Crusher (HP/CS Series)
• Applicable: Scenarios where the raw materials supply a small amount of hardware or have high requirements for production capacity stability.
• Model example: HP300 (processing capacity 120-200t/h, output particle size ≤38mm)
• Advantages: long wear-resistant parts consumption, suitable for continuous high-intensity operation; Disadvantages: secondary investment.
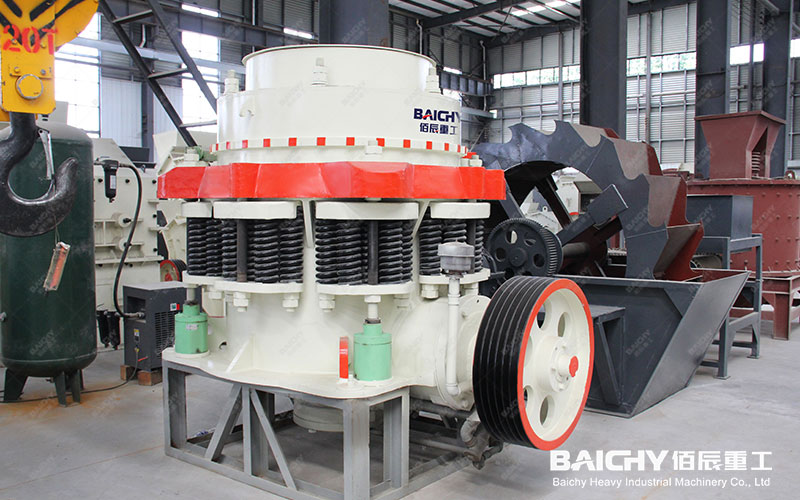
3. Fine crushing and shaping (optional)-Impact crusher (VSI series)
• Applicable scenarios: need to produce 0-5mm machine-made sand or finely adjust the particle size.
• Example: VSI1140 (processing capacity 100-260t/h)
• Advantages: The finished sand has excellent grading, suitable for high value-added products.
Stone crushing plant equipment that can crush 100,000 tons of limestone per year
• Feeding equipment: vibrating feeder (ZSW series) to ensure uniform feeding.
• Screening equipment: circular vibrating screen (YK series), to achieve multi-stage screening (such as 3YK2160).
• Pipeline equipment: conveyor pipeline (width 500-800mm), matching the production capacity of each section.
• Dust removal system: pulse bag dust collector, to meet environmental emission requirements.
Production line configuration suggestions
• Classic solution: graded crushing + reaction crushing + vibrating screen (three-stage crushing + screening)
• Applicable scenarios: production of 0-5mm sand and 5-31.5mm aggregate, with low comprehensive investment.
• High-yield solution: mold crushing + cone crushing + sand making machine (including closed-loop circulation)
• Applicable scenarios: high production capacity demand or small amount of hard rock supplied by raw materials, stability is prioritized.
Precautions
• Raw material characteristics: detect the compressive strength (usually ≤150MPa) and mud content of limestone in advance to prevent sticky material accumulation.
• Particle size control: If the product is cement raw material, coarse crushing to ≤50mm is sufficient; if it is aggregate, fine crushing stage needs to be added.
• Energy saving and consumption reduction: Use variable frequency motor and optimize crushing chamber design to reduce power consumption per ton (target: 1.5-2.0kWh/t).
• Maintenance plan: Regularly check the plates, hammers and other wearing parts, and reserve 10%-15% spare parts budget.