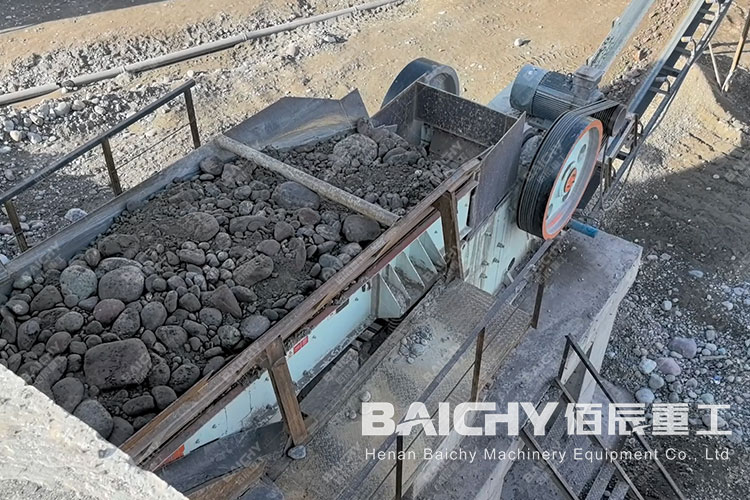
The selection of a jaw crusher for crushing concrete is a comprehensive process that requires consideration of multiple factors to ensure the most suitable equipment is selected. Here are some key selection steps and considerations:
Material characteristic analysis:
● First, the physical properties of the concrete are analyzed, including its hardness, moisture, particle size distribution, and whether it contains impurities. These characteristics will directly affect the crushing efficiency and wear degree of the crusher.
● For concrete with higher hardness, you need to choose a crusher with stronger crushing capacity, while for concrete with higher humidity, you need to consider the anti-sticking and anti-clogging capabilities of the equipment.
Production demand analysis:
● Depending on the size of the project and production needs, determine the amount of concrete that needs to be processed per hour. This will directly affect the selection of the crusher, including the size of the feed port, the adjustment range of the discharge port, and the motor power.
● Make sure the processing capacity of the selected crusher can meet production needs, and consider a certain margin to deal with production fluctuations.
Equipment size and configuration:
● Consider the layout and floor space of the crusher in the production line to ensure that the size of the equipment matches other equipment in the production line.
● According to production needs, select the appropriate adjustment range of the discharge port to flexibly adjust the product particle size.
● Consider the motor power and energy consumption of the crusher and select equipment that meets energy efficiency standards and can meet production needs.
Wear parts and wear resistance:
● Pay attention to the wearing parts of the crusher, such as jaw plates, liners, etc., and choose materials with good wear resistance to extend the service life of the equipment.
● Consider the replacement cycle and cost of wearing parts so that they can be maintained in a timely manner and reduce operating costs during production.
maintenance:
● Choose a crusher that is easy to maintain and maintain to reduce downtime and increase productivity.
● Consider the reliability and stability of the equipment and choose a manufacturer with good after-sales service and technical support.
Environmental protection and safety:
● Make sure the selected crusher meets environmental requirements, such as noise control, dust emissions, etc.
● Consider the safety performance of the equipment, such as protective measures, emergency shutdown devices, etc., to ensure production safety.
Cost-benefit analysis:
● Conduct a cost-benefit analysis by comprehensively considering factors such as the price, performance, maintenance costs, and service life of the equipment.
● Choose a cost-effective crusher to ensure that you can meet production needs while reducing operating costs.
To sum up, the selection of a jaw crusher for crushing concrete is a comprehensive process, that requires comprehensive consideration of material characteristics, output requirements, equipment size and configuration, wearing parts and wear resistance, maintenance and upkeep, and environmental protection. factors such as safety and cost-effectiveness. Through scientific selection, you can choose the crusher that best suits the project needs, improve production efficiency, and reduce operating costs.