For the small portable rock crusher (equipped with fine ore hopper module) with a capacity of 60 tons/hour required in small gold mining scenarios, the following is a professional design plan and analysis:
Core equipment configuration and function
1. Rock crusher body
- Type: It is recommended to use a jaw crusher or a hammer crusher, taking into account high crushing ratio and portability.
- Feed inlet size: Optimized to 400x600mm, suitable for common ore sizes in gold mines (such as gold-bearing quartz vein ore).
- Discharge particle size: adjustable range 10-50mm (with subsequent fine ore processing module).
- Power: Diesel/electric motor dual drive (diesel engine power is about 75-90kW, electric motor optional 55kW), adapt to the unstable power environment in the mining area.
2. Fine ore hopper module
- Function: Integrated vibrating screening system (screen aperture 5-10mm), directly separating fine ore (<10mm) into the storage hopper, reducing the need for secondary crushing.
- Capacity: Designed to be 5-8m³, ensuring continuous operation buffer and avoiding frequent shutdowns.
- Sorting optimization: Spiral chute or centrifugal concentrator interface can be added to directly connect to the gold mine gravity concentrator process to improve recovery rate.
3. Portable design
- Modular structure: The main machine, hopper, and power unit can be quickly disassembled and assembled, suitable for standard container or flatbed trailer transportation (machine weight ≤15 tons).
- Hydraulic outriggers: Equipped with an automatic leveling system, site deployment can be completed within 30 minutes.
- Tire/track option: Tracked mobile chassis (climbing ability ≥25°) is provided for complex terrain.
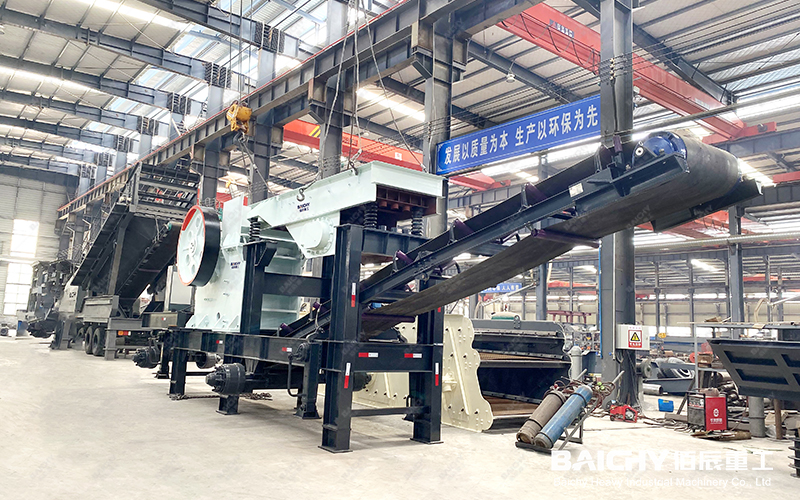
Applicable scenarios and advantages
- Adaptation to gold mine characteristics:
- Efficiently process gold-containing oxide ores, quartz vein ores and other medium and low hardness materials to avoid over-crushing and loss of gold particles.
- Fine ore hopper directly screens fine gold ore particles, and cooperates with amalgamation or cyanide leaching process to shorten the extraction cycle.
Supporting suggestions
1. Pretreatment equipment: Use a small jaw crusher as the primary crushing (if the original ore size is >400mm) to form a two-stage crushing process.
2. Ore dressing extension: Connect a shaking table or jig to form an integrated mobile production line of "crushing-screening-sorting".
3. Tailings management: Modular dewatering screen + filter press is recommended to achieve dry stacking of tailings and reduce environmental pollution.
Case reference
- A placer gold mine project in Peru: Using similar configuration equipment, the average daily processing capacity is 1,200 tons, the gold recovery rate is increased from 65% of the traditional process to 82%, and the labor cost is reduced by 40%.
- Small vein mines in West Africa: crawler crusher + fine ore bucket combination, completed the mine site migration twice within 3 months, adapted to the flexible mining needs during the exploration period.
This solution significantly improves the mining efficiency and precious metal recovery rate of small gold mines through the combination of high mobility design and refined sorting module, especially suitable for mining areas with dispersed resources and weak infrastructure. It is recommended to further optimize the crushing parameters according to the hardness of the ore and the gold content, and configure rapid detection equipment to adjust the process in real time.