The cost of a 5,000 t/d iron ore concentrator is affected by many factors, including ore type, grade, process flow, equipment selection, geographic location, etc. The following is a typical cost estimation framework and reference range:
Iron ore concentrator main equipment composition
Ore processing fee: including pre-processing links such as crushing, screening, and grinding.
Ore dressing agent cost: flotation commonly uses collectors, depressants, etc., and magnetic separation agents have lower costs.
Power consumption: Grinding and concentrator equipment consume the most power, accounting for 15%–30% of operating costs.
Key variable impact
Ore type: Magnetite costs less than hematite (flotation process is more complicated).
Grade: The lower the Fe content of the ore, the lower the concentrate recovery rate and the higher the cost.
Equipment efficiency: Equipment with a high degree of automation can reduce labor and maintenance costs.
Energy price: Fluctuations in electricity prices significantly affect electricity costs.
Environmental protection requirements: The investment and operating costs of tailings dams and water treatment facilities may account for 10%-20% of the total cost.
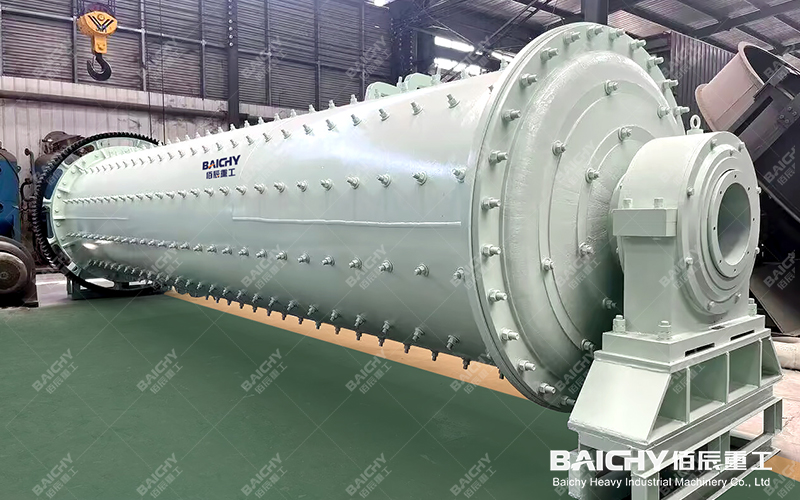
Key points for equipment selection
1. Ore properties
Hardness: Wear-resistant equipment (such as cone crushers) is required for hard rock ores, and jaw crushers can be selected for soft rocks.
Grade: Low-grade ores need to increase the grinding fineness and increase the load of flotation equipment.
Magnetic properties: Magnetite concentrators can simplify the process (omitting flotation), and hematite requires flotation.
2. Processing scale
A 5,000-ton/day concentrator needs to be matched with medium and large equipment (such as Φ3.2×4.0m ball mill) to ensure stable production capacity.
3. Degree of automation
Semi-automatic: Manual operation, low investment, suitable for small mines.
Fully automatic: PLC control, energy consumption optimization, suitable for large modern mines (cost increase of about 20%-30%).
Energy consumption and efficiency
Choose high-efficiency energy-saving equipment (such as variable frequency motors and permanent magnet separators) to reduce long-term operating costs.