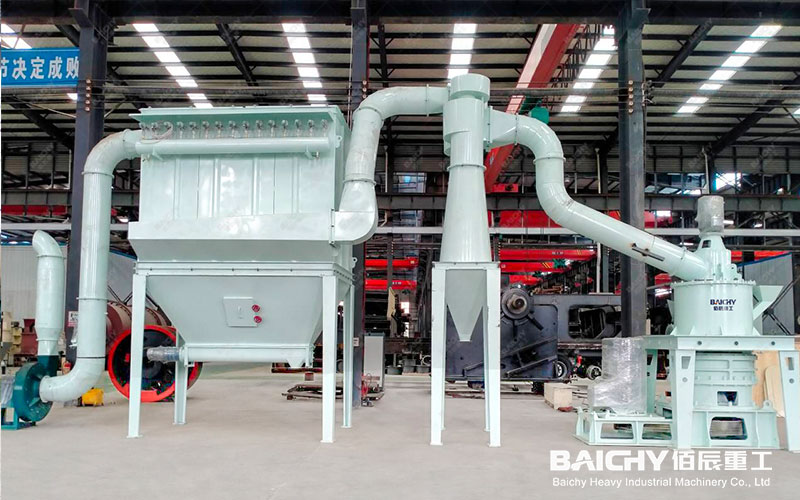
In the field of industrial manufacturing, the fineness and uniformity of powders directly determine the added value of products. From active fillers in building materials, to cathode materials in new energy batteries, to ultrafine raw materials in food and medicine, the market demand for 200-2500 mesh ultrafine powders continues to rise. However, traditional grinding equipment generally has pain points such as high energy consumption, uneven particle size, and complex maintenance, which seriously restricts the production capacity and profit space of enterprises.
HGM micron mill was born in response to the trend! As a representative of the fourth generation of ultrafine grinding technology, it provides a full-process solution from coarse grinding to ultrafine powder processing for mining, chemical, new materials and other enterprises with modular design, intelligent control system, and micron-level crushing accuracy.
HGM micron mill: technical parameters and core performance
1. Equipment introduction
HGM micron mill adopts a vertical roller mill structure, integrating the four functions of crushing, grinding, grading, and collection, and realizes efficient material crushing through the rolling shear force of multi-layer grinding rings and grinding rollers. Its core breakthroughs are:
● Improved classification accuracy: Equipped with a dynamic turbine classifier, the powder fineness can be freely adjusted between 200-2500 meshes, with a 97% finished product pass rate.
● Capacity leap: The processing capacity of a single machine covers 0.5-22 tons/hour, which is 30%-50% higher than similar equipment.
● Energy saving and consumption reduction: Unit energy consumption is reduced by 40%, and the annual electricity cost saving exceeds 200,000 yuan (taking 300 mesh calcium carbonate powder as an example).
2. Technical Parameters Overview
Project |
Parameter Details |
Feed Particle Size |
≤20mm |
Finished Product Fineness |
200-2500 mesh (5-74 microns) |
Processing Capacity |
0.5-22 tons/hour (depending on material properties) |
Main Motor Power |
55-315kW (multiple models available) |
Occupancy Area |
15-50㎡ (compact design) |
Five core advantages unlock new value of powder processing
1. Ultrafine grinding, controllable particle size
Adopting multi-level layered grinding technology, the fineness distribution of the finished product is precisely controlled by adjusting the roller pressure and the speed of the classifier. It is especially suitable for micron-level processing of high-hardness materials (Mohs hardness ≤7), such as quartz sand, calcite, barite, etc.
2. Intelligent control, worry-free and labor-saving
PLC central control system: real-time monitoring of current, temperature, vibration and other parameters, automatic adjustment of feeding speed and grinding pressure, and avoid overload shutdown.
Remote operation and maintenance support: Fault warning and remote diagnosis can be achieved through the IoT module to reduce unplanned shutdowns.
3. Energy saving and environmental protection, cost reduction and efficiency improvement
Low wear design: The grinding roller and grinding ring are made of high chromium alloy + ceramic composite material, which extends the service life by 3 times and reduces the annual maintenance cost by 60%.
Pulse dust removal system: Dust emission concentration ≤20mg/m³, in line with EU CE environmental protection standards.
4. Modular structure, flexible adaptation
Support customized configuration: According to the characteristics of the raw materials, select drying, disintegration, surface modification and other modules to meet the processing needs of special powders (such as high-purity silicon micropowder and nano-coating materials).
5. Wide material adaptability
Material type |
Typical application cases |
Non-metallic minerals |
2500 mesh paint filler made of limestone |
Metal oxides |
Preparation of raw materials for alumina ceramic substrates |
Chemical raw materials |
Ultrafine grinding of flame retardant magnesium hydroxide |
Agricultural and sideline products |
Nano-processing of starch and plant fibers |
Three major application scenarios drive industrial upgrading
1. Mining deep processing: from "extensive mining" to "high-value utilization"
● Case: A large calcite mining company introduced the HGM-1680 model to process the raw ore into 1250 mesh paint-grade heavy calcium, and the annual output value increased by 2.8 times.
2. New energy materials: Assisting the upgrading of lithium battery/photovoltaic industry
● Key applications: micron-level grinding of graphite negative electrode materials and homogenization of lithium iron phosphate positive electrode materials.
3. Environmental protection and circular economy: resource utilization of solid waste
● Innovative solutions: Preparation of permeable bricks with recycled micro-powders of construction waste and replacement of cement admixtures with micro-powders of steel slag.
From "extensive production" to "fine operation", HGM micron mill is redefining the boundaries of industrial powder processing. Choosing HGM is not only choosing a piece of equipment, but also choosing a sustainable leading competitiveness. Let us work together to create macro business value with micron-level precision!
Why choose HGM micron mill?
1. 3000+ successful cases around the world
From the palm shell fiber crushing project in Southeast Asia to the high-end calcium carbonate filler production line in Northern Europe, HGM equipment has won a good reputation for its stability.
2. Full life cycle service
Pre-sales: free material testing and process design
During sales: engineers stationed in the factory for installation and commissioning
After-sales: 2-hour response, 48-hour on-site maintenance
3. Flexible cooperation model
Support equipment procurement, financial leasing, EPC general contracting and other forms of cooperation to reduce customers' initial investment pressure.
Get exclusive quotes and technical solutions for HGM micron mills now!
If you have further requirements for the performance, capacity or application scenarios of HGM micron mills, our professional team will provide you with one-to-one service, quickly output accurate quotes and customized solutions! Here is your next action guide:
How to get a quote? 3 easy steps!
Submit requirements
Tell us your:
● Material type (such as limestone, barite, graphite, etc.)
● Target fineness (mesh or micron requirements)
● Daily average capacity requirements (tons/hour or annual output)
● Special requirements (such as explosion-proof design, food grade certification, etc.)
Free testing and solution design
● We can provide free material crushing tests (send samples to the laboratory and feedback data within 3 working days).
● Engineers will match the best model for you (HGM80/HGM100/HGM1680, etc.) based on the test results, and plan the production line layout.
Get accurate quotes
● Based on the configuration plan, provide a transparent list of equipment prices, freight, installation and commissioning costs, etc.
Support installment payment or financial leasing cooperation model.
Why choose Baichy Heavy Industry?
1. Deep technical accumulation, industry leading
● 20 years of R&D experience: Focus on deep technology in the field of mining machinery, and accumulate rich industry insights and solutions.
● 56 patented technologies: Covering key links such as equipment design and production process, reflecting continuous innovation capabilities and technical barriers.
● Market-proven star products: PFL series equipment has sold more than 5,000 units worldwide, with stable and reliable performance to meet diversified production needs.
2. Guaranteed service, worry-free for customers
① Extremely fast response mechanism:
● Engineers provide 7×24-hour online technical support to solve emergencies as soon as possible.
● Any site in the world within 48 hours to minimize losses.
②Long-term cost advantage:
● Core components are guaranteed for one year to reduce the maintenance cost of young people.
● Accessories are supplied at cost price for life to eliminate the problem of price compensation for late replacement.
3. Globalization, adapting to extreme working conditions
● Covering 150+ countries and regions: including Southeast Asia, Africa, South America and other markets, the verification equipment is widely applicable.
● Extreme environment test: It can still operate stably under groundwater conditions such as high temperature, high humidity, and high special zone, and has strong technical reliability.
4. Full-cycle service support to help efficient operation
● From installation to training: Provide professional on-site guidance installation and worker operation training to ensure rapid production of equipment.
● After-sales system: Improve maintenance, technical upgrade support, long-term operation of efficient equipment, and extend service life.
● Rights protection: Directly connect through official channels (official website: http:www.baichychina.com/WhatsApp:+86 15093222637) to avoid intermediate risks and enjoy genuine services.