Raymond mill is a commonly used industrial grinding equipment, mainly used for grinding non-metallic minerals (such as limestone, calcite, barite, dolomite, etc.). Regarding the grinding of 250-500 micron (μm) raw materials to a particle size range of 90-150 microns, the following is a detailed description of its working principle, key parameters and adjustment methods:
1. Working principle of Raymond mill
Grinding process: The material enters the mill through the feeding system and is crushed by the rolling action of the grinding roller and the grinding ring. The grinding roller presses the grinding ring tightly under the action of centrifugal force, and the material is gradually refined under the rolling and shearing force.
Grading system: The ground powder is brought into the classifier by the airflow and sorted by the centrifugal force generated by the rotating blades. The coarse particles are thrown back to the grinding chamber for re-grinding, and the fine powder enters the collection system (such as a cyclone separator or dust collector) through the classifier.
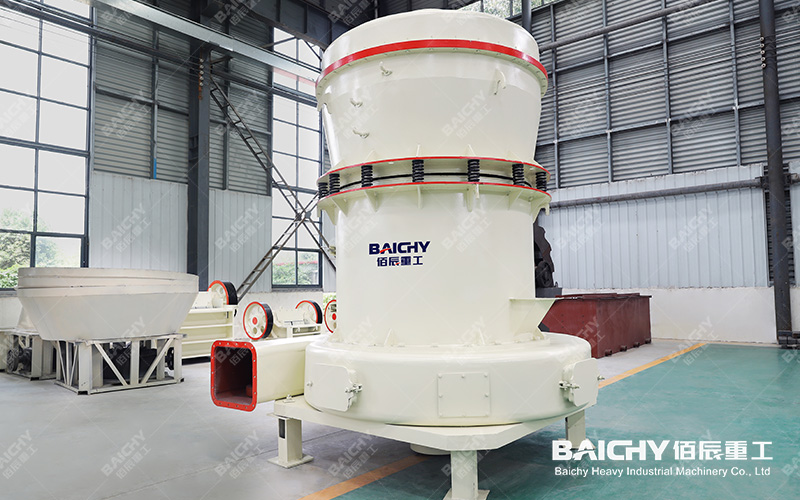
2. Key parameters for achieving particle size conversion from 250-500μm to 90-150μm
(1) Grinding roller pressure and speed
Adjusting the grinding roller pressure: Increasing the hydraulic system pressure can increase the grinding pressure of the grinding roller on the material, improve grinding efficiency, and make the powder finer. However, it is necessary to balance the pressure and equipment wear.
Grinding roller speed: The higher the speed, the more times the grinding is done per unit time, and the finer the fineness. However, it is necessary to avoid excessive speed that leads to increased energy consumption or equipment vibration.
(2) Classifier speed
Classifier blade speed: Reducing the classifier speed will reduce centrifugal force and allow larger particles to pass (increasing the finished product particle size); increasing the speed will sort out finer powder. For the target of 90-150μm, the speed needs to be adjusted to the appropriate range through experiments (usually combined with material characteristics).
(3) Air volume control
Fan air volume: Increasing the air volume will speed up material circulation, but may reduce the grinding time, resulting in an increase in coarse particles; reducing the air volume will extend the residence time of the material in the grinding chamber and improve the fineness. Need to be adjusted in coordination with the classifier.
(4) Feed particle size and uniformity
Raw material pre-screening: Ensure that the feed particle size is ≤500μm to avoid blockage by large particles or increase the grinding burden.
Uniform feeding: Control the feed speed through the vibrating feeder to prevent the mill from overloading or insufficient grinding.
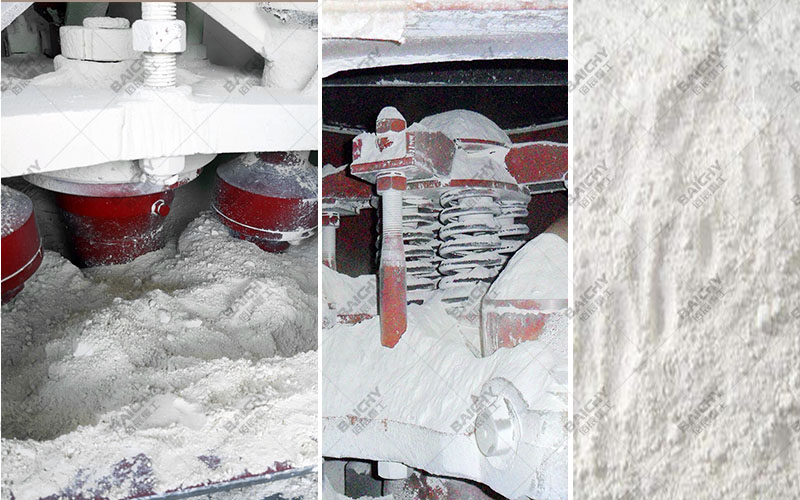
3. Operation process optimization
• Initial adjustment parameters: Set the roller pressure, classifier speed and air volume to the middle value according to the material hardness (Mohs hardness ≤7) and the target particle size.
• Trial operation and testing: Take samples to test the finished product particle size (such as laser particle size analyzer). If there are too many coarse particles (>150μm), increase the classifier speed or reduce the air volume; if there are too many fine powders (<90μm), adjust in the opposite direction.
• Dynamic balance: Maintain a balance between grinding efficiency and finished product quality to avoid excessive pursuit of fineness leading to excessive energy consumption or reduced output.
4. Applicable materials and precautions
· Applicable materials: non-metallic minerals (Mohs hardness ≤ 7), dry materials with humidity < 6%.
Precautions:
· Avoid metal impurities from entering the mill and damaging the grinding roller and grinding ring.
· Regularly check the wear of wearing parts (grinding roller, grinding ring, scraper) and replace them in time.
· Control the humidity of the material. Excessive humidity will cause the powder to adhere to the grinding chamber and reduce efficiency.
5. Typical configuration examples
Equipment model: 4R3220 Raymond mill
Motor power: 37-45kW
Processing capacity: 1-8 tons/hour (depending on the material and fineness requirements)
Finished product particle size: 80-325 mesh (about 180-45μm), which can be stabilized at 90-150μm through adjustment.
By adjusting parameters reasonably and matching material characteristics, Raymond mill can efficiently achieve particle size conversion from 250-500μm to 90-150μm. It is recommended to combine experimental data optimization during the commissioning phase to achieve the best economy and product quality.