Rotary Dryer is a kind of equipment used to remove moisture from materials. It is widely used in agriculture, industry, chemical industry, food processing and other fields. Rotary Dryer evaporates the moisture in the material by heating, ventilation or other means to achieve the purpose of drying. There are many types and designs of dryers. Different types of dryers can be selected according to different materials and process requirements.
Rotary dryer:
Working principle: By rotating the cylinder, the material is constantly turned in the cylinder and contacted with hot air to achieve the drying effect.
Application: Suitable for granular and powdery materials such as wood chips, mineral sand, chemical raw materials, etc.
Dryer is very suitable for drying wood chips. Wood chips are usually dried using rotary dryers or fluidized bed dryers. The specific choice depends on the characteristics of the wood chips and production requirements.
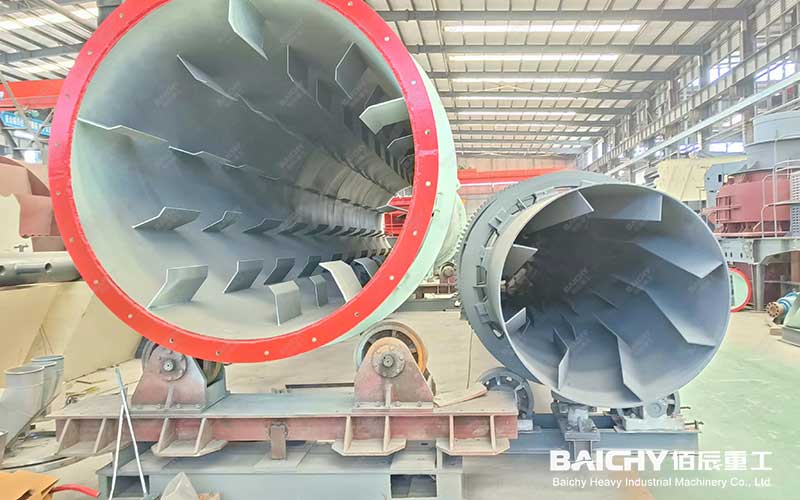
The specifications and operating parameters of the direct thermal wood chip rotary dryer are as follows:
1. Equipment type
- Dryer type: direct thermal rotary dryer
- Material: wood chips
2. Processing capacity
- Operating speed: 18 tons/hour
3. Heat source
- Heat source type: boiler flue gas
- Flue gas temperature: 20°C (this may be wrong, usually the boiler flue gas temperature is higher, it may be above 150°C)
4. Dryer specifications
- Diameter: usually between 2-4 meters depending on the processing capacity and material characteristics
- Length: usually between 10-20 meters
- Rotation speed: usually between 3-10 rpm (revolutions per minute)
- Tilt angle: usually between 1-5 degrees to facilitate material flow
5. Temperature control
- Inlet temperature: usually between 150-400°C depending on the boiler flue gas temperature
- Outlet temperature: Usually between 80-120°C, depending on the final moisture content requirements of the wood chips
6. Power system
- Motor power: usually between 30-100 kW depending on the size and load of the dryer
- Drive mode: usually gear drive or chain drive
7. Material
- Cylinder material: usually heat-resistant steel or carbon steel, lined with wear-resistant materials
- Support structure: steel structure to ensure stability and durability
8. Control system
- Automation degree: can be equipped with PLC control system to achieve automatic operation and monitoring
- Sensor: temperature sensor, humidity sensor, pressure sensor, etc.
9. Environmental protection measures
- Dust removal system: usually equipped with cyclone separator or bag dust collector to reduce dust emission
- Exhaust gas treatment: may be equipped with flue gas treatment system to reduce pollutant emissions
10. Safety measures
- Explosion-proof measures: due to the possibility of dust generated during the drying process of wood chips, explosion-proof devices are required
- Emergency shutdown: Equipped with emergency stop button to ensure safe operation
11. Maintenance and care
- Lubrication system: Regularly lubricate bearings and transmission parts
- Inspection frequency: Regularly check the cylinder, support structure and transmission system to ensure the normal operation of the equipment
12. Installation and commissioning
- Foundation requirements: A solid concrete foundation is required to ensure stable operation of the equipment
- Commissioning cycle: Usually 1-2 weeks are required for commissioning and optimization
Notes
- Flue gas temperature: If the boiler flue gas temperature is only 20°C, it may not be enough to effectively dry the wood chips, and a higher temperature is usually required.
- Material properties: The initial moisture content, particle size and density of the wood chips will affect the design and operating parameters of the dryer.