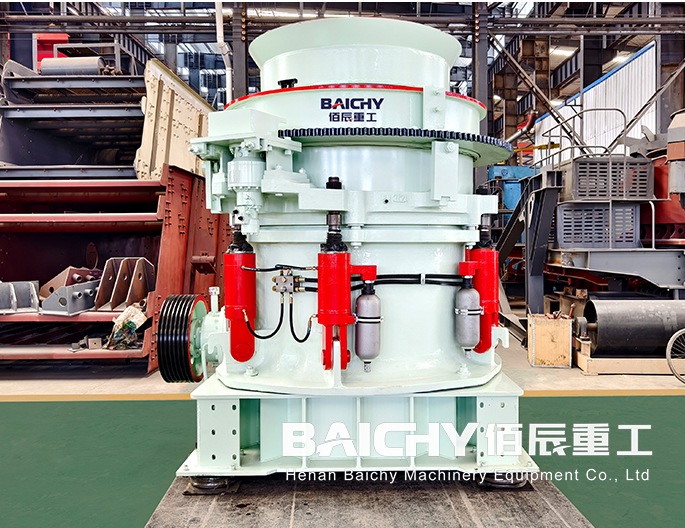
The HPC series hydraulic cone crusher has a higher speed combined with stroke, which greatly increases the rated power and passing capacity of the crusher, thereby improving the crushing ratio and production efficiency.
The crusher has a reasonable structure, advanced crushing principles and technical parameters, reliable operation, and low operating costs. All parts of the crusher have wear-resistant protection, which reduces maintenance costs to a minimum, and the general service life can be increased by more than 30%.
By adopting a special crushing chamber designed using the inter-granular lamination principle and a matching rotation speed, the traditional single-particle crushing principle is replaced to achieve selective crushing of materials. This significantly improves the fine material ratio and cube content of the product and greatly reduces needle and flake materials.
The HPC series hydraulic cone crusher provides a variety of crushing cavity types to choose from, such as A-type cavity for medium crushing, B-type cavity for medium-fine crushing, C-type cavity for fine crushing, and D-type cavity The cavity is for extra fine crushing to meet flexible applications of different materials and crushing needs.
Model | Cavity | Standard type | Shorthead type | Capacity(t/h) | Motor Power(kw) | ||
---|---|---|---|---|---|---|---|
Feeder opening size(mm) | Outlet setting size(mm) | Feeder opening size(mm) | Outlet setting size(mm) | ||||
HPC-500 | Coarse | 285 | 25 | 90 | 13 | 400-790 | 355-450 |
Medium | 200 | 20 | 55 | 10 | 335-610 | ||
Fine | 133 | 16 | 40 | 8 | 280-460 | ||
UltrafineFine | 95 | 13 | 35 | 6 | 180-435 |
NO. | Product Name | Model | Quantity |
---|---|---|---|
1 | Hopper | - | 1 |
2 | Vibrating feeder | ZSW1349 | 1 |
3 | Jaw CrusherC | 125 | 1 |
4 | HP Cone Crusher | HPC-500 | 1 |
5 | DG Cone Crusher | DG400 | 1 |
6 | YK Vibrating Screen | 4YK2460 | 4 |
7 | YK Vibrating Screen | YK1860 | 1 |
7 | Belt conveyor | B1200 | - |
1. Raw material processing: The large pieces of wool less than 1250mm that have been blasted or excavated and mined are fed to the raw material warehouse through a dump truck.
2. Coarse crushing: The raw materials are evenly supplied to the jaw crusher for primary crushing through the rod feeder with a pre-screening function.
3. Medium and fine crushing: After being crushed by the jaw crusher, the 100-250mm semi-finished materials are transported to the cone crusher for secondary crushing through a belt conveyor.
4. Screening: After secondary crushing, the 6-45mm mixed finished aggregate is transported to the screening workshop through a belt conveyor for classification and screening. The screened materials that do not meet the particle size requirements will be returned to the fine cone crusher for recycling until they meet the requirements.
5. Finished product transportation: Qualified finished products that meet customer needs are transported to the finished product silo through a belt conveyor.
The specific 500T/H hard rock aggregate production line plan may vary depending on customer needs, raw material characteristics, production environment, and other factors. Therefore, in practical applications, it needs to be designed and adjusted according to specific conditions.
Thank you for your interest in Baichy Machinery. If you want to know more about our crushers and industrial grinding equipment.
Contact us now to find out what we can do for you!