For the 5-10 t/h vertical roller mill, clinker is used as raw material and cement powder is the final product. The following is a detailed analysis of the equipment and its production process:
Overview of vertical roller mill
Vertical roller mill, referred to as vertical mill, is a high-efficiency equipment integrating fine crushing, drying, grinding and conveying. It is mainly used for grinding various materials of different strength, hardness and water content, such as clinker, gypsum, quartz sand, etc. With its advantages of high efficiency, energy saving and environmental protection, vertical roller mill has been widely used in cement, building materials, chemical industry and other industries.
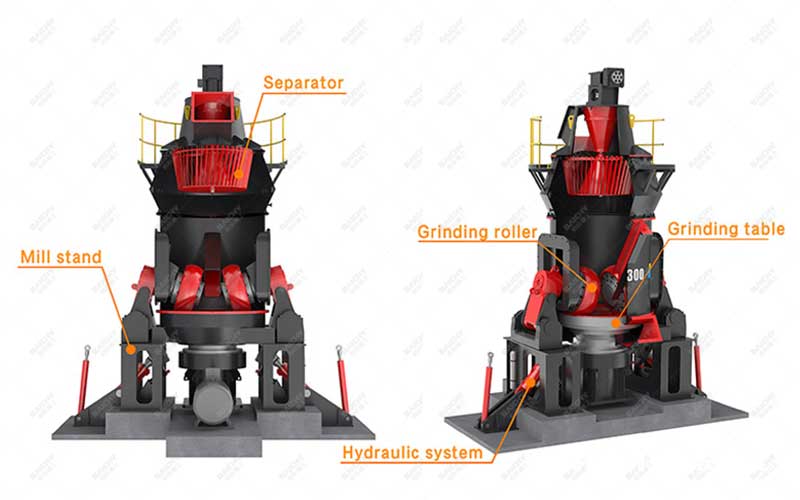
Working principle of vertical roller mill
The working principle of vertical roller mill is relatively simple and efficient. The main motor drives the grinding disc to rotate through the reducer, and the hot air enters the vertical mill body from the air inlet. The raw materials (such as clinker) fall to the center of the grinding disc through the discharge pipe. The uniformly rotating grinding disc uses centrifugal force to evenly disperse and flatten the raw materials outward to form a material bed of a certain thickness. The material bed is rolled and rolled by multiple grinding rollers on the grinding disc. Under the push of centrifugal force, the raw materials continue to move toward the outer edge of the grinding disc. When the fly ash leaving the grinding disc encounters the hot air entering the mill through the air ring, it rises through the middle shell of the mill and enters the separator. In this process, the coal powder and the hot air undergo sufficient heat exchange, and the water evaporates rapidly. The finished product particle size is controlled at the outlet of the powder selector. Particles larger than the specified particle size are separated and fall back to the grinding disc for further grinding. Cement powder that meets the fineness requirements enters the dust collector through the powder selector and is finally sent to the finished product bin.
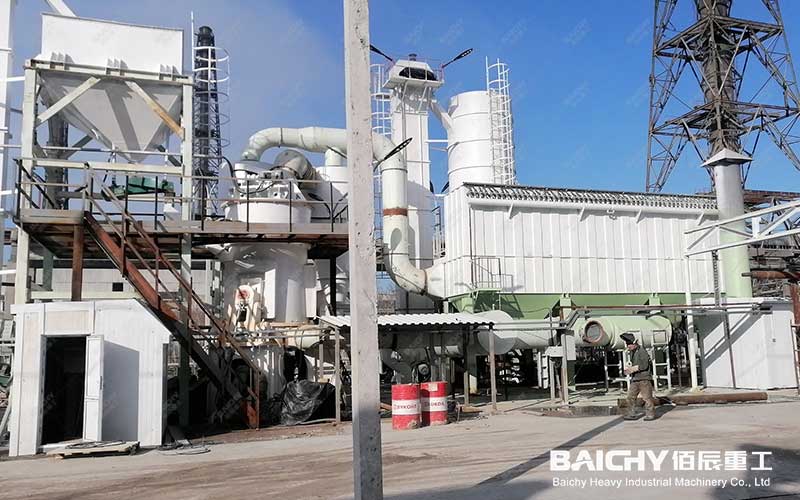
Advantages of vertical mill
1. High grinding efficiency: The vertical mill adopts the material bed grinding principle, with high grinding efficiency and system energy consumption 20%~35% lower than that of the ball mill.
2. Strong drying capacity: Materials with a moisture content of 12%~20% can be dried in the vertical mill, and there is no need to set up a raw material drying system.
3. Large particle size of materials entering the mill: The maximum particle size of materials entering the mill can reach about 4%~5% of the diameter of the grinding roller, generally 40~100mm. Large and medium-sized vertical mills can omit the third-level crushing in some cases.
4. Uniform particle grading: The material stays in the vertical mill for a short time (generally 2~3 minutes), and qualified products can be separated in time to avoid over-grinding.
5. Low noise: The grinding roller and the grinding disc are not in direct contact during operation, and the noise is 20~25 decibels lower than that of the ball mill.
6. Low wear and high utilization rate: The unit product wear is generally 5-10g/t. When grinding cement raw materials, the life of the roller sleeve and liner is more than 8000 hours, and the operation rate can reach 95%.
7. Less dust and clean operating environment: The vertical mill adopts an overall sealing design, and the system operates under negative pressure, with less dust and a clean operating environment.
8. Simple process flow: After large-scale production, the material particle size is large and the process flow is simple. Large and medium-sized vertical mills can replace the three-stage fine crushing and ball milling systems.
9. Small footprint: The building area of the vertical mill is about 70% of the ball mill, and the building space is about 50%~60% of the ball mill system.
Application of vertical mill in cement grinding
Vertical mill has significant advantages in cement grinding. Since the vertical roller mill can efficiently grind raw materials such as clinker, and the product fineness is controllable and the particle size distribution is uniform, it is very suitable for the production of cement powder. In addition, the drying capacity of the vertical roller mill also enables it to handle raw materials with high water content, thereby simplifying the production process.
5-10 tons/hour vertical roller mill has the advantages of high efficiency, energy saving and environmental protection in the production of cement powder with clinker as raw material. In practical applications, the appropriate vertical roller mill model and parameters should be selected according to specific production needs, and the production process should be optimized to ensure product quality and production efficiency.