In response to the needs of a 60-100tph (tons per hour) andesite crushing plant in Indonesia, and the specific requirements of product output sizes of 10-20mm and 16-31.5mm, the following is an overview of the crushing plant design based on these parameters:
Selection of andesite crushing equipment
Jaw crushers are used for the coarse crushing stage of andesite.
1. Features: The cavity is deep, there is no dead zone, it is suitable for processing large-size raw materials, and it is not easy to clog.
2. Adjustment range: The discharge port is adjusted by a hydraulic motor, which is convenient for adjusting the product particle size.
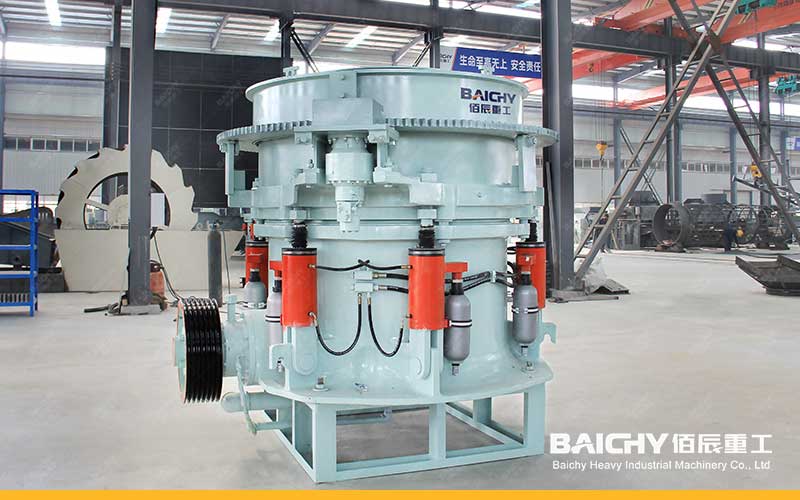
Cone crushers are used in the secondary crushing stage to further refine the material output by the jaw crusher.
1. Features: Strong compressive resistance, suitable for processing rocks with moderate hardness such as andesite.
2. Adjustment range: The product particle size can be controlled by adjusting the parameters of the cone crusher.
Screening equipment is used to screen the crushed material into products of different particle size ranges.
Features: High efficiency and precision, the screen aperture can be adjusted as needed.
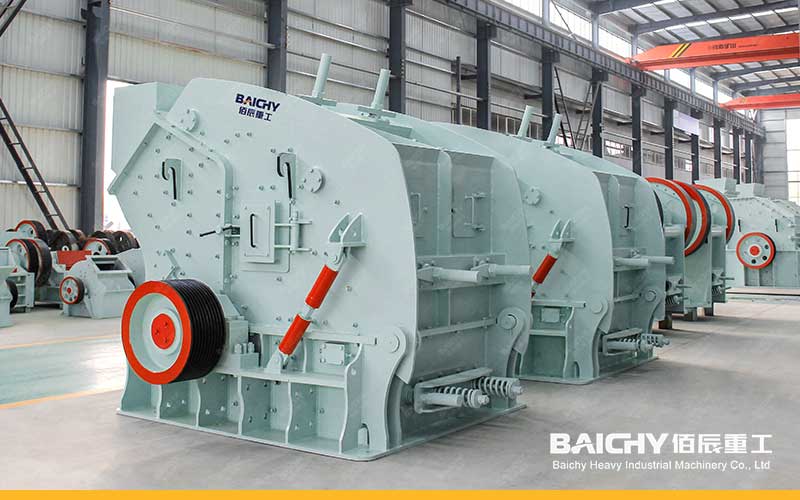
Impact crusher (optional)
If a finer product size or higher sand making demand is required, consider using an impact crusher for fine crushing.
Features: fine output size, good particle shape, suitable for high-standard material requirements.
Crushing process design of andesite crushing equipment
1. Raw material preparation, after natural andesite is mined, use a feeder to evenly feed it into a jaw crusher.
2. In the coarse crushing stage, andesite is coarsely crushed in a jaw crusher to produce materials with larger particle sizes.
3. In the medium crushing stage, the coarsely crushed materials are sent to a cone crusher for medium crushing to further refine the particle size.
4. In the screening stage, the materials after medium crushing are screened using a vibrating screen. According to product requirements, the materials are screened into products with two particle size ranges of 10-20mm and 16-31.5mm.
5. Finished product output The screened products are sent to the finished product pile for transportation or further processing.
Andesite Crushing Equipment Equipment Configuration and Capacity
According to the capacity demand of 60-100tph, select the appropriate crusher model and quantity.
The specific configuration of the crusher equipment should be comprehensively considered according to the actual site conditions, raw material characteristics, product requirements and other factors.
Precautions for the selection of andesite crushing equipment
1. Equipment selection The selection of crushing equipment should consider factors such as the equipment's processing capacity, wear resistance, and maintenance cost. Priority should be given to equipment produced by well-known brands and reputable manufacturers.
2. Crushing process The design of the crushing process should consider factors such as the particle size distribution, hardness, and water content of the raw materials. The particle size range and quality of the product should be strictly controlled during the crushing process.
3. Environmental protection and safety The crushing plant should establish complete environmental protection facilities, such as dust removal equipment, noise control equipment, etc. The safety production regulations should be strictly observed to ensure the safety of personnel and equipment.
For the needs of Indonesia's 60-100tph andesite crushing plant, jaw crushers, cone crushers, and screening equipment can be selected for crushing and screening operations. Through reasonable equipment configuration and process design, the requirements of product output size of 10-20mm and 16-31.5mm can be achieved. At the same time, attention should be paid to equipment selection, crushing process, environmental protection and safety issues to ensure the stable operation and efficient output of the crushing plant.
Related recommendations: Andesite Aggregate Crushing Plant In Indonesia