The coal mill of a power plant is one of the indispensable key equipment in the process of coal-fired power generation. Its main function is to grind coal into powder to facilitate combustion in the boiler and improve combustion efficiency. The following are some detailed introductions about coal grinding machines in power plants:
Structure and composition:
Grinding disc: As the core component of the coal mill, the grinding disc is disc-shaped and usually made of cast iron. The grinding disc is surrounded by grinding rollers, and the coal is crushed and ground on the grinding disc through high-speed rotation.
Feeding device: responsible for feeding coal between the grinding disc and grinding roller for crushing and grinding. Common feeding devices include drum feeding devices and liquid balance feeding devices, which adjust the feeding amount and speed to ensure that coal is evenly distributed within the coal mill to improve efficiency and crushing.
Transmission system: transmits the power of the motor to the grinding plate and grinding roller to realize their rotation. Generally, hydraulic transmission, gear transmission or chain transmission are used to ensure the normal operation and efficient work of the coal mill.
Discharge device: Located at the edge of the grinding plate, the ground coal is discharged from the grinding plate and transported to downstream equipment through the conveying device for further processing and utilization.
Other components: also include cross-flow plates, distribution plates, wind systems, motors, control systems, etc.
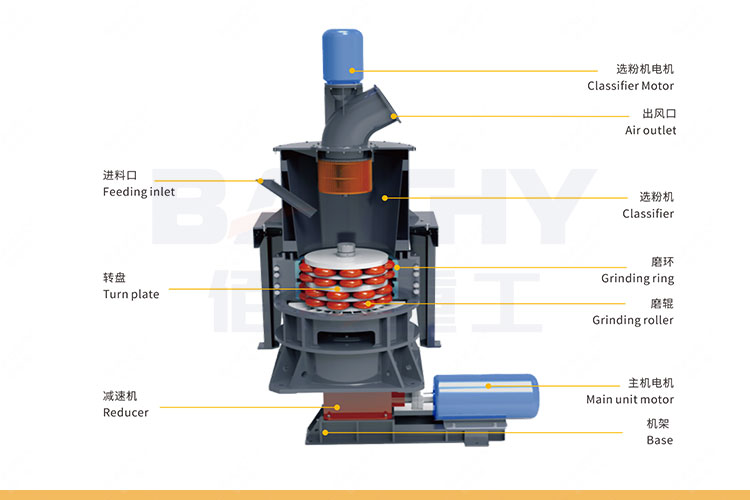
2. working principle:
• After the coal enters the coal mill, it is first evenly fed into the center of the grinding disc by the feeding device.
• The pressure exerted by the millstone distributes the coal across the millstone.
• The grinding roller is located above the grinding disc and drives the rotation of the grinding roller through a transmission device.
• During the operation of the coal mill, the grinding roller moves cyclically along the circumferential direction of the grinding disc, exerting pressure and shearing force on the coal at the same time, causing the coal to be ground and pulverized.
• The ground coal is discharged through the discharging device and sent to downstream equipment.
3. Type of coal mill:
According to different working principles and structures, coal mills can be divided into various types such as ball mills, roller mills, roller mills, hammer mills, and air separation coal mills. Each type has its unique characteristics and applicable scenarios.
4. Application scenarios:
In addition to coal-fired power plants, coal mills are also widely used in the metallurgical industry, chemical industry, and other fields. For example, in the steel production process, a large amount of coke is used, and the coal mill can grind the coal into coke suitable for smelting; in the chemical production process, the coal mill can grind the coal into pulverized coal suitable for production.
5. Advantages and Disadvantages:
Different types of coal mills have different advantages and disadvantages. For example, ball mills have the advantages of continuous operation and high production efficiency, but they are noisy, consume high energy, and produce a large amount of dust; roller mills can better control the powder quality, have high precision, and low energy consumption, but have high requirements for rollers and cams. The processing accuracy requirements are higher.
To ensure normal operation and extend the service life of the coal mill, the power plant needs to perform regular maintenance and upkeep of the coal mill. At the same time, when selecting a coal grinder, it is necessary to comprehensively consider its type, performance, cost, and other factors according to the actual situation to select the most suitable coal grinder equipment.